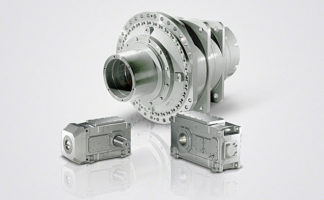
8/9
Siemens NC 62 · 2016
Lifecycle Services
SINUMERIK Manufacturing Excellence
Extended Machine Contracts
8
■
Overview
Calculable costs for maintenance and service
This is what we are offering to machine tool manufacturers,
machine distributors and machine tool users with the Extended
Machine Contracts option.
In these individually agreed contracts, maintenance concepts
are assembled from the following modules: preventative mea-
sures, repair, access to Siemens service personnel, service
intervals, and spare parts logistics/management.
Here, Siemens accepts the risk of costs through fixed-price
invoicing of the services provided (contract cost). With the sole
objective of providing tailor-made, efficient support with mainte-
nance.
You remove the risk of unexpected costs and can rely on a high
degree of machine availability. The joint agreement ensures ac-
cess to qualified Siemens service personnel for fault elimination
on site as well as professional spare parts logistics, which en-
sures proximity to the customer.
Additional advantages:
•
Security of planning, reduced costs and transparency of costs
•
Higher productivity thanks to minimal downtimes
•
Service packages tailored to requirements
•
Supplementing and supporting the service personnel at the
manufacturer or end user
•
Access to the worldwide service structure of Siemens AG
Repair Service Contract RSC:
Subsequent repairs at fixed prices
We have developed the Repair Service Contract RSC especially
for machine manufacturers and machine distributors. It offers
subsequent rectification of defects at the site of the machine at
fixed prices. With these contract-based services, you can cover
the personnel costs and materials costs that are incurred for
rectifying any faults on our products after the second commis-
sioning phase at the end customer. The service period can be
freely selected.
The personnel services comprise the provision of service per-
sonnel, error diagnostics and fault rectification on site as well as
verification of fault rectification. The runtime of the contract can
extend the period of liability for defects to up to 5 years.
In the case of services that exceed the RSC scope, you can use
the regional service or add-on services. This includes extended
service periods, agreed response times and preventative
measures.
The benefits of the Repair Service Contract RSC:
•
Risks that result from liability for defects are limited by
fixed prices
•
Fault rectification at the installation site of the machine, without
the need for verification of the defect by the machine tool
manufacturer or distributor
•
Reduced downtimes at the customer site due to stored
product data and final destination information
■
Overview
(continued)
LSC local service contract: the modular service package
With the LSC local service contract, we offer machine users an
individual, modular service package that ensures the availability
of machine tools and manufacturing systems to a considerable
extent and therefore makes an important contribution to efficient
production.
The scope of the service contract is individually matched to
the service concept. We can also offer you our contract-based
services outside normal office hours – up to 24 hours a day,
365 days a year. Alternatively, we can offer you our services with
faster response times: from the normal "next day" to a 4-hour
response time.
The benefits of the local service contract LSC:
•
Assured availability through reduction of the machine
downtimes
•
Plannable costs thanks to agreed service contract prices
•
Services tailored to requirements
Life Cycle Check
Our Life Cycle Check service assists you in optimizing your
spare parts strategy so as to safeguard your productivity.
Life Cycle Check – Data acquisition
Acquisition of all modules in your installation which have control
or drive relevance.
Life Cycle Check – Analysis
•
The acquired Siemens modules are analyzed with respect to
their availability as a spare/replacement or repair part. Infor-
mation about estimated phase-out and discontinuation dates
and possible follow-on types is collected and recorded in a
report.
•
Support for an optimum spare parts strategy:
- Demand-based ordering of the Siemens spare parts service
- Optimization of customer's spare parts inventory
(stock reduction)
- Buyback of spare parts by Siemens on request
- Punctual availability of upgrades
- Definition of follow-on solutions/general overhaul
- Retrofit scheduling
As part of the local service contract, a Life Cycle Check analysis
is performed once a year and we will send you a report which
specifies the spare parts availability of your components which
you can use as a guide for adjusting your spare parts inventory.
The Benefits of the Life Cycle Check:
•
Increased productivity because plant outages are rare: An
optimized spare parts supply keeps downtimes to a minimum
•
Reduction in asset and warehousing costs:
Use of the Siemens spare parts service
•
You only store selected spare parts on site:
Reduce stocks of superfluous parts
•
Extension of the plant lifecycle:
Installation of suitable follow-on types
We also offer further services – for example, we compare the
components in your spare parts stores with the components
installed on your machines and inform you by way of a report of
any components held in your stores which have become obso-
lete for your machines. Or we will show you which of the stored
components are compatible as spare parts so that you can
reduce your inventory accordingly.
■
More information
Please contact your local Siemens sales office or Regional
Company for more information.
Contact information can be found on the Internet at:
/automation/partner
© Siemens AG 2016