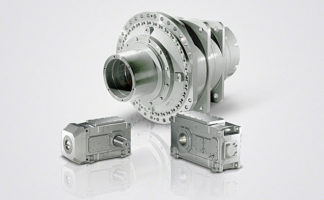
2/18
Siemens NC 62 · 2016
SINUMERIK CNC
SINUMERIK Safety Integrated
2
■
Overview
SINUMERIK Safety Integrated provides integrated safety
functions that support the implementation of highly effective
personnel and machine protection. The safety functions comply
with the requirements of Category 3 as well as Performance
Level PL d according to EN ISO 13849-1 and safety integrity
level SIL 2 according to EN 61508. Consequently, important
functional safety requirements can be implemented easily and
economically. Available functions include, among others:
•
Functions for safety monitoring of velocity and standstill
•
Functions for establishing safe boundaries in work spaces
and protected spaces, and for range recognition
•
Direct connection of all safety-related signals and their internal
logical linkage
■
Benefits
7
High level of safety:
Complete implementation of the safety functions in
Category 3/SIL 2/PL d
7
High level of flexibility:
Supports the implementation of practically sound safety and
operating concepts
7
Extremely cost-effective:
Reduced hardware and installation costs
7
Enhanced availability:
Absence of interference-susceptible electromechanical
switching elements
■
Function
The safety functions are available in all modes and can
communicate with the process using safety-oriented input/
output signals.
They can be implemented for each individual axis and spindle:
Safety Integrated drive-based (basic version)
•
Safe Torque Off (STO)
Suppression of drive pulses, providing safe electronic
interruption of the energy supply
•
Safe Brake Control (SBC)
Safe (2-channel) control of a holding brake (integrated in the
SINAMICS S120 Motor Module)
•
Safe Stop 1 (SS1)
Safe shutdown of a drive followed by STO
Safety Integrated system-integrated (option)
•
Safe shutdown
Ensures safe transition of the drive from motion to standstill
when a monitoring device or a sensor (e.g. a light barrier)
responds.
•
Safe braking ramp (SBR)
Monitoring of the speed curve. The speed must be reduced
after a stop request has been issued
•
Safe operating stop (SBH)
Monitors drives for standstill. The drives remain fully functional
in closed loop position control
•
Safe standstill (SH)
Suppression of drive pulses, providing safe electronic
interruption of the energy supply
•
Safely limited speed (SLS)
Monitoring of configurable speed limits
•
Safety-related output
n
<
n
x
Safe speed recognition of a drive
•
Safe software limit switches (SE)
Variable traversing range limitations
•
Safe software cams (SN)
Range recognition
•
Safety-related input/output signals (SGE/SGA)
Interface with process
•
Safe programmable logic (SPL)
Direct connection of all safety-related signals and their internal
logical operation
•
Safe brake management (SBM)
- 2-channel braking signal
(integrated in the SINAMICS S120 Motor Module) (SBC)
- Cyclic brake test (SBT)
•
Safety-related communication via standard bus
- Connection of distributed I/O for process and safety signals
via PROFIBUS/PROFINET using the PROFIsafe protocol.
- Safety-related CPU - CPU communication via PROFIBUS or
PROFINET
•
Integrated acceptance test
Partially automated acceptance test for all safety-related
functions. Simple operation of the test process, automatic
configuration of Trace functions and automatic generation of
an acceptance record.
© Siemens AG 2016