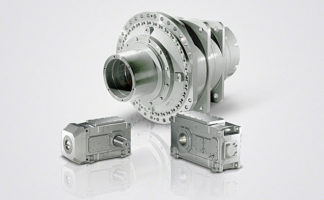
5/143
Siemens NC 62 · 2016
5
SINAMICS S120 drive system
Measuring systems
Built-on optoelectronic rotary encoders
> Absolute encoders
■
Function
Absolute encoders with SSI/EnDat and PROFIBUS DP at the top, and
DRIVE-CLiQ and PROFINET IO at the bottom
Absolute encoders (absolute shaft encoders) are designed on
the same scanning principle as incremental encoders, but have
a greater number of tracks. For example, if there are 13 tracks,
then 2
13
= 8192 steps are coded in the case of single-turn en-
coders. The code used is a one-step code (gray code) which
prevents any scanning errors from occurring.
After the machine is powered up, the position value is trans-
ferred immediately to the controller. There is no need for homing.
Absolute encoders with DRIVE-CLiQ, SSI and EnDat are of
advantage in time-critical applications.
In plants with a large number of encoders, encoders with
PROFIBUS DP and PROFINET IO are more advantageous due
to the reduced wiring overhead. Encoders with PROFIBUS DP
are parameterizable and support isochronous mode with direct
data exchange. The encoders with PROFINET IO are also
parameterizable, additionally have two ports and support the
RT and IRT operating modes.
Single-turn encoders
Single-turn encoders divide one rotation (360 degrees mechan-
ical) into a specific number of steps, e.g. 8192. A unique code
word is assigned to each position. After 360° the position values
are repeated.
Multi-turn encoders
Multi-turn encoders record the number of revolutions in addition
to the absolute position within one revolution. To do this, further
code discs which are coupled via gear steps with the encoder
shaft are scanned. When evaluating 12 additional tracks, this
means that 2
12
= 4096 revolutions can be coded.
■
Technical specifications
1)
Observe the max. permissible cable length of the connected module.
Article No.
6FX2001-5.D..-0AA1
6FX2001-5.S..
6FX2001-5.E..
Product designation
Absolute encoder with
DRIVE-CLiQ
Absolute encoder with
SSI
Absolute encoder with
EnDat
Operating voltage DC
V
p
on encoder
V
24
- 15 % + 20 %
10 ... 30
5
± 5 %
Current consumption, approx.
• Single-turn
mA
245
160
160
• Multi-turn
mA
325
200
200
Interface
DRIVE-CLiQ
SSI
EnDat
Clock input
–
Differential cable receiver
acc. to EIA standard RS 485
Differential cable receiver
acc. to EIA standard RS 485
Data output
DRIVE-CLiQ
Differential cable driver
acc. to EIA standard RS 485
Differential cable driver
acc. to EIA standard RS 485
Short-circuit strength
Yes
Yes
Yes
Transmission rate
Mbit
100
–
–
kHz
–
100 … 1000
100 ... 2000
Speed, max.
• Electrical
rpm
14000
–
–
-
At ± 1 bit accuracy
rpm
–
5000
5000
-
At ± 100 bit accuracy
rpm
–
10000
10000
• Mechanical
- Single-turn
rpm
12000
12000
12000
- Multi-turn
rpm
10000
10000
10000
Cable length to downstream
electronics, max.
1)
m (ft)
100 (328)
–
–
• Up to 100 kHz cycle
m (ft)
–
400 (1312)
–
• Up to 300 kHz cycle
m (ft)
–
100 (328)
150 (492)
• Up to 1 MHz cycle
m (ft)
–
50 (164)
50 (164)
© Siemens AG 2016