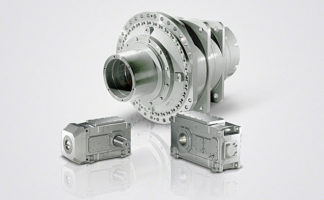
5/139
Siemens NC 62 · 2016
5
SINAMICS S120 drive system
Measuring systems
Built-on optoelectronic rotary encoders
■
Overview
The built-on optoelectronic rotary encoders sense distances,
angles of rotation or speeds in machines. They can be used in
conjunction with numerical control systems, programmable logic
controllers, drives and position displays, e.g. for:
•
SINUMERIK CNC controls
•
SIMOTION Motion Control Systems
•
SIMATIC programmable logic controllers
•
SINAMICS drive systems
■
Application
A distinction is made between incremental and absolute
measuring procedures:
•
In the case of incremental encoders, the machine must travel
to a reference point after each power-off state, as the position
is not usually stored in the controller, and movements of the
machine while the power is off are not recorded.
•
Absolute encoders, on the other hand, also record these
movements while the power is off and return the actual
position after power on. Travel to a reference point is not
necessary.
■
Design
All encoders are available in Synchro flange and clamp flange
versions. Encoders with a Synchro flange can be attached to the
machine with 3 clamps or mounted with axial screws. The en-
coder is driven by means of a plug-in coupling or a spring disk
coupling. Alternatively, pulleys can also be used.
The encoder supply voltage is 5 V DC or alternatively 10 V to
30 V DC. The 10 V to 30 V DC version supports longer cable
lengths. Most control systems supply the voltage directly at the
measuring circuit connector. With SINAMICS, the power supply
for the measuring systems is provided via the Sensor Modules.
For rotary encoders with cables, the cable length including the
connector is 1 m (3.28 ft).
The following bending radii must be observed for the cable to
the encoder:
•
One-time bending:
≥
20 mm (0.79 in)
•
Continuous bending:
≥
75 mm (2.95 in)
© Siemens AG 2016