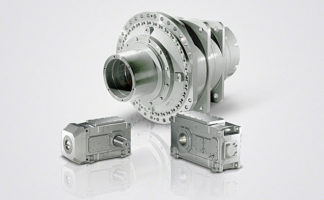
5/129
Siemens NC 62 · 2016
5
SINAMICS S120 drive system
Encoder system connection
Encoder system connection
■
Overview
Motors with DRIVE-CLiQ interface
DRIVE-CLiQ is the preferred method for connecting the encoder
systems to SINAMICS S120.
Motors with DRIVE-CLiQ interface are available for this purpose,
e.g.
•
1PH8/1FT7/1FK7 synchronous motors
•
1PH8 asynchronous motors (induction motors)
Motors with a DRIVE-CLiQ interface can be directly connected
to the associated Motor Module via the available
MOTION-CONNECT DRIVE-CLiQ cables. The connection of the
MOTION-CONNECT DRIVE-CLiQ cable at the motor has degree
of protection IP67.
The DRIVE-CLiQ interface supplies power to the motor encoder
via the integrated 24 V DC supply and transfers the motor en-
coder and temperature signals and the electronic rating plate
data, e.g. a unique identification number, rating data (voltage,
current, torque) to the Control Unit. This means that for the
various encoder types – e.g. resolver or absolute encoder –
different encoder cables with varying permissible lengths
are now no longer required; just one cable type,
MOTION-CONNECT DRIVE-CLiQ with varying permissible
lengths, can be used for all encoders.
Motors with DRIVE-CLiQ interface simplify commissioning and
diagnostics, as the motor and encoder type are identified
automatically.
Motors without DRIVE-CLiQ interface
The encoder and temperature signals of motors without
DRIVE-CLiQ interface, as well as those of external encoders,
must be connected via Sensor Modules. Sensor Modules
Cabinet-Mounted are available in degree of protection IP20
for control cabinet installation, as well as Sensor Modules
External in degree of protection IP67.
Only one encoder system can be connected to each Sensor
Module.
■
Technical specifications
Motors with DRIVE-CLiQ interface
■
More information
Motor encoder and temperature signals must be connected
when possible to the corresponding Motor Module or Power
Module and external encoders to the Control Unit. However,
the DRIVE-CLiQ connections can also be bundled via
DRIVE-CLiQ Hub Modules.
Safety Integrated
The Safety Integrated Extended Functions of the
SINAMICS S120 drive system require suitable encoders.
Motor driven by belt
Unfavorable material combinations generate static electricity
between the belt pulley and the belt. Electrostatic charging must
be prevented, since this can discharge via the motor shaft and
the encoder, thereby causing disturbances in the encoder
signals. One remedy is to use an anti-static belt.
Built-in encoder systems
• Incremental encoder 22 bit
(resolution 4,194,304, internal
2048 S/R) + commutation position
11 bit (encoder IC22DQ)
• Absolute encoder 22 bit single-
turn (resolution 4,194,304, internal
2048 S/R) + 12 bit multi-turn
(traversing range 4096 revolu-
tions) (encoder AM22DQ)
• Absolute encoder 20 bit single-
turn (resolution 1,048,576, internal
512 S/R) + 12 bit multi-turn
(traversing range 4096 revolu-
tions) (encoder AM20DQ)
• Absolute encoder 16 bit single-
turn (resolution 65,536, internal
32 S/R) + 12 bit multi-turn
(traversing range 4096 revolu-
tions) (encoder AM16DQ)
• Absolute encoder 15 bit single-
turn (resolution 32,768, internal
16 S/R) + 12 bit multi-turn
(traversing range 4096 revolu-
tions) (encoder AM15DQ)
• Resolver 15 bit (resolution 32,768,
internal, multi-pole) (R15DQ)
• Resolver 14 bit (resolution 16,384,
internal, 2-pole) (R14DQ)
Power requirement at 24 V DC,
max.
(supply via
MOTION-CONNECT
DRIVE-CLiQ cable)
190 mA
Cable length, max.
• When using
MOTION-CONNECT 500
DRIVE-CLiQ cables
100 m (328 ft)
• When using
MOTION-CONNECT 800
DRIVE-CLiQ cables
50 m (164 ft)
© Siemens AG 2016