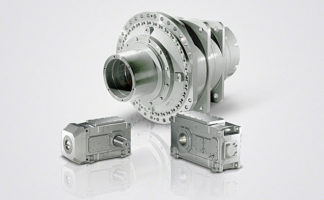
5/127
Siemens NC 62 · 2016
5
SINAMICS S120 drive system
Supplementary system components
Hydraulic Linear Actor (HLA module)
■
Overview
Hydraulic Linear Actor (HLA module)
The 2-axis HLA module is a DRIVE-CLiQ component for control
cabinet installation.
•
From a topology viewpoint, the HLA module can be viewed as
a hydraulic double-axis Motor Module. The HLA module is an
interface module for the I/O components of a hydraulic linear
drive.
•
The HLA module therefore functions in a similar way to a
Terminal Module. This module can be used for a variety of
different purposes in the SINAMICS S120 drive line-up.
■
Benefits
7
Closed-loop control for up to two hydraulic axes
7
Parallel operation of hydraulic and electrical drives
7
Closed-loop velocity and force control
7
Safety Integrated functions
■
Application
• Presses
•
Rotary indexing machines
•
Forming machines
•
Bending technology
■
Function
The HLA module has been designed to control (open-loop and
closed-loop) electro-hydraulic control valves of hydraulic linear
axes in conjunction with the SINUMERIK 840D sl. Up to two
hydraulic axes can be controlled by this module.
To control a hydraulic linear drive, a control unit is required
in addition to the HLA module. This unit can be either the
NCU 7x0.3B PN, an NX or a CU320-2 Control Unit which
operates under the control of a SINUMERIK 840D sl system.
By combining a control unit with the HLA module, it is possible
to create a highly dynamic, electro-hydraulic control circuit.
A hydraulic linear axis can be combined and interpolated with
other hydraulic or electrical axes on one SINUMERIK 840D sl.
The HLA module requires a 24 V supply. This power supply is
used to internally supply the HLA module and is also required by
various sensors.
The HLA module generates the power supply for the control
valves and the shutoff valves from an external DC voltage supply
(e.g. SITOP) with a rated voltage of 26.5 V.
The purely hydraulic components, designed for CNC operation,
must be supplied by the user.
■
Function
(continued)
Interfaces:
•
4 DRIVE-CLiQ sockets
•
1 × 24 V for the electronics power supply
•
1 × 26.5 V to supply the hydraulic components
•
2 TTL/SSI encoder connections (1 per axis)
•
6 pressure sensor inputs (3 per axis)
•
2 control valve connections (1 per axis)
•
2 shutoff valve outputs (1 per axis)
•
2 terminals for valve spool sensors of the shutoff valves
(1 per axis)
•
2 EP terminals (1 per axis)
■
Technical specifications
■
Selection and ordering data
Article No.
6SL3420-2HX00-0AA0
Product designation
Hydraulic Linear Actor
(HLA module)
Electronics power supply
• Voltage
V
DC
20.4 ... 28.8 (24 – 15 % + 20 %)
• Current, max.
A
DC
1.1
• Power loss, max.
W
12
Supply of hydraulic
components
• DC voltage
V
DC
26 ... 27 (26.5
±
2 %)
• Direct current, max.
A
DC
8.5 A
• Temperature range
°C (°F)
0 ... 55 (32 ... 131)
(with derated output current
for the control valves)
Max. cable lengths
m (ft)
40 (131)
• to valves
• to sensors
• to encoder (SSI, TTL)
DRIVE-CLiQ cables/
encoders
m (ft)
100 (328)
24 V, 26.5 V and
EP terminals
m (ft)
10 (32.8)
PE/ground connection
At the housing with M5/3 Nm screw
Net weight (without
mating connector)
kg (lb)
1.75 (3.86)
Degree of protection
IP20
Environmental
conditions
Climatic environmental
conditions
• Long-term storage in the
transport packaging
Class 1K4 to EN 60721-3-1
Temperature: -25 ... +55 °C
(-13 ... +131 °F)
• Transport in the transport
packaging
Class 2K4 acc. to EN 60721-3-2
Temperature: -40 ... +70 °C
(-40 ... +158 °F)
• Operation
Temperature: 0 ... 55 °C
(32 ... 131 °F)
1)2)
Relative humidity: 5 ... 95 %
Oil mist, salt mist, ice formation,
condensation, dripping water,
spraying water, splashing water
and water jets are not permitted
Description
Article No.
Hydraulic Linear Actor
(HLA module)
2-axis controller
Two-axis version (can also be
used for single-axis drives)
With one measuring system for
direct position sensing per axis
6SL3420-2HX00-0AA0
1)
Current derating above 40 °C (104 °F) at the control valve output
2)
At altitudes exceeding 1500 m (4921 ft) above sea level, the upper
temperature limit must be reduced by 3.5 °C (38.3 °F) / 500 m (1640 ft).
© Siemens AG 2016