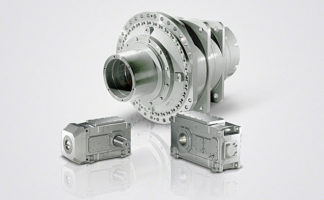
5/25
Siemens NC 62 · 2016
5
SINAMICS S120 drive system
Control Units
CU320-2 Control Units
■
Overview
The communication, open-loop and closed-loop control func-
tions for one or more Motor Modules and the Line Module are
executed in a CU320-2 Control Unit. The CU320-2 Control Unit
is essentially designed for multi-axis operation.
CompactFlash card for CU320-2 Control Units
The CompactFlash card contains the firmware and set parame-
ters. The CompactFlash card is plugged into the appropriate slot
on the CU320-2 Control Unit.
A CU320-2 Control Unit can perform the communication, open-
loop and closed-loop control functions for several Motor Mod-
ules. The computing capacity required increases in proportion
to the number of connected Motor Modules and system compo-
nents and in relation to the dynamic response required. For the
CU320-2 Control Unit, the performance expansion is required for
machines with 4 axes or more. The utilization of the CU320-2
Control Unit can be calculated with the SIZER engineering tool.
In addition to the firmware, the CompactFlash Card also con-
tains licensing codes which are required to enable firmware
options.
■
Overview
(continued)
In addition to the Article No., the following firmware options can
currently be ordered with or without performance
expansion:
•
Safety Integrated Extended Functions, order codes per axis
F01 to F06
•
High output frequency
1)
, order code
J01
The firmware options can also be enabled on-site, for example,
if the performance expansions required are not known at the
time of placing the order or the Safety Integrated Extended
Functions are to be enabled retrospectively. You will need the
serial number of the CompactFlash card and the Article No. of
the firmware option to be enabled. With this information, you can
purchase the associated license code from a license database
and enable the firmware option. The license code is only valid for
the CompactFlash card declared and cannot be transferred to
other CompactFlash cards.
■
Design
CU320-2 Control Units feature the following interfaces as
standard:
•
4 DRIVE-CLiQ sockets for communication with other
DRIVE-CLiQ devices, e.g. Motor Modules, Active Line
Modules, Sensor Modules, Terminal Modules
•
CU320-2 PN: 1 PROFINET interface with 2 ports
(RJ45 sockets) with PROFIdrive V4 profile
•
CU320-2 DP: 1 PROFIBUS interface with
PROFIdrive profile V4
•
12 parameterizable digital inputs (floating)
•
8 parameterizable bidirectional digital inputs/outputs
(non-floating)
•
1 serial RS232 interface
•
1 interface for the BOP20 Basic Operator Panel
2)
•
1 slot for the CompactFlash card on which firmware and
parameters are stored
•
1 slot for mounting an option module (e.g. TB30 Terminal
Board)
•
2 rotary coding switches for manually setting the PROFIBUS
address
•
1 Ethernet interface for commissioning and diagnostics
•
3 measuring sockets and one reference ground for
commissioning support
•
1 connection for the electronics power supply via the 24 V DC
supply connector
•
1 PE connection
•
1 ground connection
A shield connection for the signal cable shield on the option
module is located on the CU320-2 Control Unit.
The available option slot is used to expand the interfaces, for
example, to include additional terminals or for communication
purposes.
The status of the CU320-2 Control Unit is indicated via multi-
color LEDs.
As the firmware and parameter settings are stored on a plug-in
CompactFlash card, the Control Unit can be changed without
the need for software tools.
The CU320-2 Control Unit can be mounted on the side of the
Line Module in booksize format via brackets integrated in a Line
Module. The CU320-2 Control Unit can also be fixed to the wall
of the control cabinet using the integrated fixing lugs. As the
CU320-2 Control Unit is not as deep as the Line Modules,
suitable spacers are available to increase the depth of the
CU320-2 Control Unit to 270 mm (10.63 in).
1)
For more information, see
2)
BOP20 is not used on machine tools.
© Siemens AG 2016