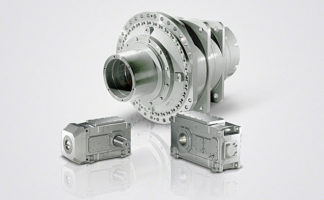
5/8
Siemens NC 62 · 2016
5
SINAMICS S120 drive system
Introduction
Power Modules
The simplest version of a SINAMICS S120 drive system consists
of a CU310-2 Control Unit and a Power Module. A line rectifier, a
voltage-source DC link and an inverter for supplying a motor are
integrated in the Power Module.
Power Module in blocksize format with CU310-2 PN Control Unit
Power Modules are designed for single drives which are not
capable of regenerating energy to the supply. Generated energy
produced during braking is converted to heat in braking resis-
tors.
Power Modules can also be operated by a CU320-2 Control Unit
or a drive control integrated in SINUMERIK, e.g. in configura-
tions where a single drive has been added to a multi-axis drive
group. In this case, the Power Modules in blocksize format must
be equipped with the CUA31 Control Unit Adapter. This is con-
nected with the CU320-2 Control Unit or the NCU in SINUMERIK
using DRIVE-CLiQ. Power Modules in chassis format are directly
connected to the Control Unit using a DRIVE-CLiQ cable.
The following versions are available:
•
Motor Modules and Line Modules in booksize and chassis
formats
•
Power Modules in blocksize and chassis formats
•
Motor Modules in booksize compact format
•
SINAMICS S120 Combi
Booksize format
Booksize format units are optimized for multi-axis applications
and are mounted adjacent to one another. The connection for the
common DC link is an integral feature.
With respect to control cabinet cooling, SINAMICS S120 in
booksize format offers a number of highly effective options. De-
pending on the application, component heat loss can be trans-
ferred to the environment using three different heat dissipation
methods. The design of the components differs only in the for-
mat of the backplane and the location of the external fan module.
The front panel (where the connections are located) and the
width of the components are common to all designs.
Internal air cooling
In this standard solution, the power loss from the electronics and
power units of the drive components is removed by natural cool-
ing or by a forced-ventilation system and routed to the interior of
the control cabinet.
External air cooling
External air cooling uses the through-hole technology. The com-
ponents' power unit heat sinks pass through the mounting sur-
face in the control cabinet and can thus dissipate the heat losses
of the power circuit to a separate external ventilation circuit.
Degree of protection IP54 can be achieved at this "mechanical
interface" – the external heat sink. The heat sink, with its cooling
fins and the fan unit (part of the scope of supply), protrudes
through the back into a separate ventilation duct, which can also
be open to the outside. The only heat loss that remains in the
cabinet is largely emitted by the electronics.
M
3 ~
~
~
G_D211_XX_00042
Power
Module
Control
Unit
DRIVE-CLiQ
■
Overview
(continued)
© Siemens AG 2016