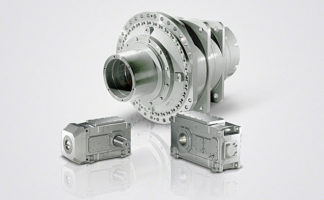
6/2
Siemens NC 82 · 2017
Measuring Systems Motion Control Encoder
Built-on optoelectronic rotary encoders
Introduction
6
■
Overview
Motion control encoders are optoelectronic built-on encoders
that detect the traversal distances, angles of rotation, speeds or
positions of machine axes. Motion control encoders are direct
measuring systems that are built-on to shafts, axes or motors.
They can be used in conjunction with numerical and program-
mable logic controllers, drives and position displays. Motion
control encoders are system-tested, certified components that
have been harmonized for use with the following systems:
•
SINUMERIK CNC controls
•
SIMOTION Motion Control Systems
•
SIMATIC programmable logic controllers
•
SINAMICS drive systems
■
Application
Motion control encoders are used with machine tools and
production machines as additional external measuring systems.
They are available as incremental or absolute encoders.
Incremental encoders
In the case of incremental encoders, the machine must travel to a
reference point after each power-off state, as the position is not
usually stored in the control. Movements of the machine while the
power is off are not recorded.
Incremental encoders are suitable for use in simple machine
concepts with mostly small dimensions.
Absolute encoders
Absolute encoders, on the other hand, also record movements
while the power is off and return the actual position after power
on. Travel to a reference point is not necessary.
Absolute encoders are suitable for complex machines or
machines with large dimensions.
■
Design
All motion control encoders are available in Synchro flange and
clamp flange versions. The absolute encoders are also available
with a hollow shaft and torque arm.
The motion control encoders are driven via a plug-in coupling or
spring disk coupling. Alternatively, pulleys can also be used.
The motion control encoder supply voltage is 5 V DC or alterna-
tively 10 V to 30 V DC. The 10 V to 30 V DC version supports
longer cable lengths. Most control systems supply the voltage
directly at the measuring circuit connector. With SINAMICS, the
measuring systems are provided with power via the Sensor
Modules.
For motion control encoders with cables, the cable length
including the connector is 1 m.
The following bending radii must be observed for the cable to
the built-on encoder:
•
One-time bending:
≥
20 mm
•
Continuous bending:
≥
75 mm
■
More information
Power supply
The measuring systems only fulfill the requirements stipulated in
the standard IEC 61010-1 if the power is supplied from a
secondary circuit with limited power according to
IEC 61010-1
3rd Ed.
, Section 9.4 or with limited power according
to IEC 60950-1
2nd Ed.
, Section 2.5, or from a secondary circuit
Class 2 according to UL1310.
You can also use the corresponding sections of the standards
DIN EN 61010-1, EN 61010-1, U 61010-1 and CAN/CSA-C22.2
No. 61010-1 instead of the standard IEC 61010-13
3rd Ed.
,
Section 9.4, respectively the corresponding sections of the stan-
dards DIN EN 60950-1, EN 60950-1, UL 60950-1 and
CAN/CSA-C22.2 No. 60950-1 instead of the standard
IEC 60950-1
2nd Ed.
, Section 2.5.
Motion Control Encoder
Interface
Built-on
encoder
applicable
for Safety
Integrated
Resolution
S/R = signals/revolution
Accuracy
arcsec
Cable length
m
Degree of
protection
at housing
(at shaft
input)
Incremental encoders
sin/cos 1 V
pp
Yes
1000 ... 2500 S/R
± 18 mech. × 3600/
PPR count
z
150
IP67
(IP64)
RS422 (TTL)
1)
500 ... 5000 S/R
± 18 mech. × 3600/
PPR count
z
100
IP67
(IP64)
Absolute encoders
DRIVE-CLiQ
Yes
Single-turn
24 bit
Multi-turn
36 bit
(24 bit single-turn +
12 bit multi-turn)
± 20
100
IP67
(IP64)
Accessories for measuring systems
Couplings
Clamps
Signal connector as mating connector
MOTION-CONNECT DRIVE-CLiQ signal cables
1)
If you require information about the usability of measuring systems Motion
Control Encoder for Safety Integrated please contact your local Siemens
office.
© Siemens AG 2016