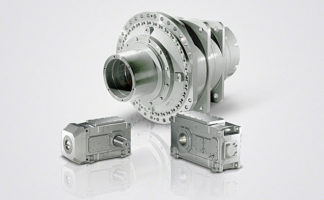
1/8
Siemens NC 82 · 2017
1
Introduction
Drive Based Safety Integrated
■
Overview
Drive Based Safety Integrated provides integrated safety
functions that support the implementation of highly effective
personnel and machine protection.
The safety functions comply with the requirements of
Category 3 as well as Performance Level PL d according to
DIN
EN ISO
13849-1 and safety integrity level SIL
2 according to
DIN EN 61508. Consequently, important functional safety
requirements can be implemented easily and economically.
The functional scope includes, for example:
•
Functions for safe monitoring of standstill
•
Functions for safe monitoring of speed
■
Benefits
7
High degree of safety:
Full implementation of the safety functions in Category 3/
SIL 2/PL d
7
Outstanding flexibility:
Application of practical safety and operating concepts
7
Faster commissioning:
Integrated safety functions
■
Application
The basic Safety Integrated functions (STO, SS1, SBC) as well
as the extended Safety Integrated functions of SINAMICS can
be used for the CNC axes of the SINUMERIK 828. The basic
Safety Integrated functions are controlled directly via terminals.
A SINAMICS S120 TM54F Terminal Module is required for
controlling the extended Safety Integrated functions.
For simple positioning tasks, e.g. revolvers, loading systems or
tool magazines that require no coordination with the CNC part
program, it is possible to connect two auxiliary axes to the
SINUMERIK 828D by means of PROFINET using a SINAMICS
CU310-2 PN or CU320-2 PN.
The basic Safety Integrated functions of the SINAMICS system
can be utilized for these CNC auxiliary axes. The basic Safety
Integrated functions are selected by hardware and in 2
channels
via terminals on the CU310-2 PN/CU320-2 PN and the Motor
Module.
A partially automated acceptance test is provided in
SINUMERIK Operate for acceptance testing Safety Integrated
functions. All measured data and traces are logged and can be
printed out in an acceptance report.
■
Design
We recommend the following safety relays for the configuration
of the safe control logic for individual safety functions:
•
SIRIUS 3SK safety relays for configuring a hardware circuit
•
SIRIUS 3RK3 Modular Safety System for a graphically
parameterizable solution
You will find further information about SIRIUS in Catalog SI 10 or
in the Siemens Industry Mall at:
/industrymall
■
Mode of operation
Clearly structured screen forms are provided in SINUMERIK
Operate to assist with the commissioning of Safety Integrated
functions.
Safety status information such as, for example, the name of the
currently active Safety Integrated function, is transferred to the
CNC via the safety info channel (SIC).
The NCK and drive can exchange signals in the opposite
direction via the safety control channel (SCC) for the purpose of
conducting the safe brake test, for example.
This solution significantly reduces the wiring outlay for the
machine manufacturer.
© Siemens AG 2016