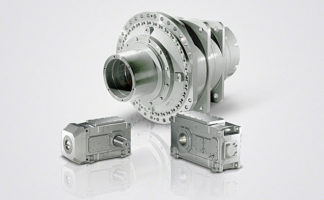
SINAMICS S150 NEMA
Introduction
1
Siemens D21.7
(Part 2) – 2015
Application of SINAMICS S150
SINAMICS S150 is an enclosed variable speed drive for high
performance stand-alone applications that may require high
dynamic performance also on weak or fluctuating power
supplies, clean power (low harmonics always meeting the
harmonic limits of IEEE 519), frequent braking at high power
levels or full regeneration of power back into the supply (4
quadrant operation). Examples of typical applications include
centrifuges, test stands, cranes and hoists, overland or
downhill conveyors, presses, cross cutters and shears.
Functionality
SINAMICS S150 includes state-of-the-art IGBT PWM inverters
on both the line side and motor side, which enables it to
transmit power in both directions, from the line to the load
or from the load back to the line, whilst operating at unity, or
leading or lagging power factor. The drive is characterized by
the following capabilities:
• Power regeneration continuously at full rated current for
braking. Dynamic braking using a braking chopper and
resistor is also optionally available, for example to enable
electrical braking of an overhauling load even in the event
of a power failure
• An innovative line side clean power filter which provides
a clean sinusoidal waveform with current and voltage
harmonics well below the most stringent limits of
IEEE 519-1992
• Operation on weak power supplies, and tolerance to
fluctuations in the line voltage or frequency without
affecting or degrading highly dynamic control of the motor.
• Operation at unity power factor (default setting), or
reactive power control (capacitive or inductive) to help
improve the facility power factor, by operating at a leading
or lagging input powerfactor
• Voltage boost operation, for example operate a motor at
460 V, 60 Hz off a 400 V, 50 Hz supply without the need for
a step-up transformer
The control can be operated in either Volts/Hertz or
sensorless vector control modes, or closed loop vector
control with encoder with the addition of optional speed
and position encoder interface boards. Siemens vector
control also allows operation down to zero speed with high
torque accuracy, without an encoder. Other control functions
include, for example:
• Critical speed avoidance (4 bands)
• Auto-restart with variable restart delay and number
of restarts
• Restart on the fly to catch a spinning motor
• Kinetic buffering where the drive draws power from
the motor while it is coasting down during a supply dip
or failure
The user friendly AOP30 operator panel with graphical LCD
and plain-text display provides easy commissioning and
parameterization using interactive menus, and alarm and
fault logs.
Benefits
• Clean power drive designed for high efficiency operation
at unity (or controllable) power factor
• Motoring or regenerating at full rated current
• All components are easily accessible, making the drive
extremely service friendly
• Increase in plant availability since individual modules and
power components can be replaced quickly and easily
• Easy commissioning and parameterization using interactive
menus on the user friendly AOP30 operator panel with
graphical LCD and plain text display
• Type tested, robust design provides guaranteed
performance in industrial environments
• A broad range of standard options to optimally configure
the drive for the required environment and application
1/5