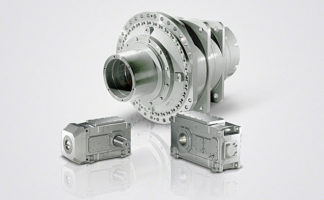
SINAMICS S150 NEMA
Engineering Information
3
Siemens D21.7
(Part 2) – 2015
3/31
Braking units
Braking units
Braking units are used when the drive needs to absorb
regenerative energy occasionally and briefly, for example
when stopping it quickly (emergency stop). The braking
units comprise a braking module and a braking resistor,
which is installed externally.
Two sizes of braking units are available for the SINAMICS
S150 enclosed drive with braking powers of 100 kW (for
150 HP & 200 HP, 460V) and 200 kW (for larger 460 V and
575V units). For higher braking powers, braking units may
be connected in parallel for larger drives (on request, not
for all ratings).
A thermal contact, which can be integrated into the drive’s
alarm and shutdown sequence, is installed in the braking
resistor for monitoring.
Determining the required braking units and braking resistors
• For periodic duty cycles with a load duration of ≤ 90 s, the
mean braking power value within this duty cycle must be
determined. The relevant period should be used as the
time base.
• For periodic duty cycles with a load duration of ≥ 90 s or
for sporadic braking operations, a 90 s time segment in
which the greatest mean value occurs should be selected.
A 90 s period should be set as the time base.
When determining the required braking unit rating (braking
module and braking resistor), consider both the mean
braking power value and the required peak braking power.
Basic Data
Supply voltage
380 V to
480 V
380 V to
480 V
500 V to
600 V
500 V to
600 V
Enclosed drive
SINAMICS S150
150 HP to
200 HP
250 HP to
1,150 HP
75 HP to
125 HP
150 HP to
1,250 HP
Braking module
Continuous power
P
DB
25 kW
50 kW
25kW
50 kW
Braking module
Power
P
40
50 kW
100 kW
50kW
100 kW
Braking module
Rated power
P
20
100 kW
200 kW
100kW
200 kW
Braking module
Peak power
P
15
125 kW
250 kW
125kW
250 kW
Braking resistor
R
B
4.4 Ω
2.2 Ω
6.8 Ω
3.4 Ω
±7.5%
±7.5%
±7.5%
±7.5%
Max. current
189 A
378 A
153A
306 A
Option code
L61
L62
L64
L65
Load diagram
Calculating the P20 power
To reduce the voltage stress on the motor and drive, the
response threshold at which the braking unit is activated
and the DC bus voltage generated can be reduced. For
example, the DC bus voltage for the drives in the voltage
range from 380 V to 480 V can be reduced from 774 V to
673 V. This also reduces the possible peak power. A factor
of 1.06, rather than a factor of 0.8 should be used.
The ON/OFF states of the braking module are controlled by
a 2-point controller. The respective response thresholds are
shown in the following table:
Drive voltage range
Braking unit response threshold
380 V to 480 V
774 V (673 V)
500 V to 600 V
967 V (841 V)
15
P
20
P
40
P
DB
P
DB
P
15
P
20
P
40
P
t
=
= 5x
= Powerwhich is permissible every 90 s for 15 s
= 4 x
= Powerwhich is permissible every 90 s for 20 s
= 2 x
= Powerwhich is permissible every 90 s for 40 s
1.00
10
20
30
40
50
60
70
80
90
100
0.75
0.50
0.25
s
1.50
1.25
DB
P
/
P
DB
P
15
DB
P
DB
P
Rated power
G_D211_EN_00013a