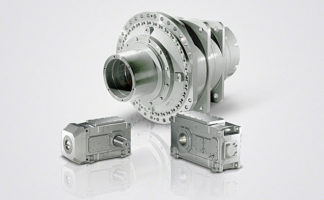
SINAMICS S150 NEMA
Engineering Information
3
Siemens D21.7
(Part 2) – 2015
Safety Integrated – Using encoders
Safe speed/position sensing with encoder
Incremental encoders or absolute encoders with
photoelectric sampling are permitted for safe sensing
of the position values on a drive. HTL/TTL incremental
encoders can also be used.
Safe actual value sensing relies on
redundant evaluation of
the incremental tracks A/B that supply sin/cos signals of 1
Vpp. Only encoders of the type whose A/B track signals are
created and processed using purely analog techniques can
be used. The encoder signals are input via the SMC20
Sensor Module Cabinet- Mounted (cabinet option
K48
).
When HTL/TTL incremental encoders are used, safe actual
value sensing is achieved by the use of two independent
encoders or special dual HTL/TTL encoders. In this case,
the minimum possible speed resolution must be taken
into account. The encoder signals are input via the SMC30
Sensor Module Cabinet- Mounted (cabinet options
K50, K52
).
When motors with a DRIVE-CLiQ interface are used, the
speed/ position actual values are generated directly in the
motor as safe values and transferred to the Control Unit
over a safe
DRIVE-CLiQ communication link. When motors
without a DRIVE-CLiQ connection are used, a Sensor Module
(SMC20/30, SME20/25/120/125) must be provided. A
separate DRIVE-CLiQ connection is required for each
measuring system.
The following can be used for safe speed/position sensing:
• Single-encoder systems or
• Dual-encoder systems
Example: Single-encoder system
In a single-encoder system, the motor encoder is used
exclusively for safe actual value sensing. In this case, the
motor encoder must be an incremental or absolute encoder
with photoelectric sampling.
Example: Dual-encoder system
With a dual-encoder system, the safe actual values for a
drive are provided by two separate encoders.
For this configuration, either two HTL/TTL encoders, one
dual HTL/TTL encoder or one HTL/TTL encoder and one
sine-cosine encoder can be used.
The encoder must be mechanically attached in such a manner
that the encoder shaft is unable to unplug or slide off.
For further information, refer to IEC 61800-5-2: 2007,
Table D.16.
A list of Siemens motors that fulfill the electrical and
mechanical requirements is available at:
Safe actual value sensing without encoder
For applications with encoderless mode or with encoders
that have no safety capability, the safety functions can also
be implemented without an encoder. It is not possible to use
all safety functions in this case.
In operation without encoder the speed actual values are
calculated from the measured electrical actual values. It is
thus possible to implement speed monitoring in operation
without an encoder.
An encoder that is used for the purposes of motor control
has no significance for the safety function here.
Safety Integrated Extended Functions “without encoder”
must not be used if the motor, after it has been switched off,
can still be accelerated by the mechanical elements of the
connected machine component.
In the hoisting gear of a crane, for example, the suspended
load can accelerate the motor as soon as the motor is
switched off. In this case, the safety functions “without
encoder” are not permitted.
By contrast, a horizontal conveyor is always braked to a
standstill due to friction as soon as the motor is switched
off. In this case, the safety functions “without encoder” may
be used.
3/26
DRIVE-CLiQ
E
M
G_D011_EN_00442
Machine table
Backlash
Sensor Module
(not applicable for motor
with DRIVE-CLiQ interface)
E = encoder
M = motor
E
M
E
DRIVE-CLiQ
G_D011_EN_00443
Sensor Module
(not applicable for motor
with DRIVE-CLiQ interface)
E = encoder
M = motor