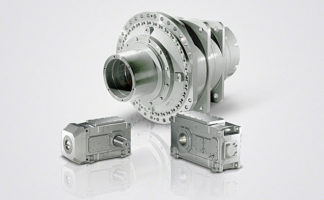
SINAMICS S150 NEMA
Engineering Information
3
Siemens D21.7
(Part 2) – 2015
3/23
Safely-Limited Speed (SLS)
The SLS function monitors the drive to ensure that it does
not exceed a preset speed limit.
Effect
The SLS function monitors the drive against a parameterized
speed limit. Four different limit values can be selected. As
with SOS, the speed setpoint is not independently influenced.
After SLS has been selected, the higher-level control must
decelerate the drive until its speed drops below the selected
speed limit within a parameterizable time. If the speed
limit is exceeded, a customizable drive-integrated fault
reaction occurs.
The SLS limit stage 1 can be multiplied by a factor that is
transferred in 16-bit resolution via PROFIsafe. This allows an
almost unlimited number of limits to be specified.
Application
The SLS function is used if people are in the danger zone
of a machine and their safety can only be guaranteed only
if the machine speed is reduced. Typical application cases
include those in which an operator must enter the danger
zone of the machine for the purposes of maintenance or
setting up, such as a winder in which the material is
manually threaded by the operator. To prevent injury to
the operator, the roller may only spin at a safely reduced
speed. SLS is often also used as part of a two-stage
safety concept. While a person is in a less critical zone, the
SLS function is activated, and the drives are only safely
stopped when the operator enters a more critical area closer
to the machine with higher potential risk. SLS can be used
not only for operator protection, but also for tool protection,
e.g. if a maximum speed must not be exceeded.
Customer benefits
The SLS function can contribute to a significant reduction in
downtime, or greatly simplify or even accelerate setup. The
overall effect achieved is a higher availability of the plant.
Moreover, external components such as speed monitors can
be omitted.
Safely-Limited Speed (SLS)
Safe Speed Monitor (SSM)
The SBT function carries out a brake function test at
regular intervals.
Effect
The proper functioning of brakes that have become worn is
checked by application of a torque to the closed brake. Drive
systems that have two brakes, e.g. motor brake and external
brake, can be tested with different torque values.
Application
The SBT function is suitable for implementing a safe brake in
combination with the SBC function.
Customer benefits
The function detects faults or wear in the mechanical
components of the brake. Automatic brake function tests
reduce maintenance overheads and increase the safety
and reliability of the machine/plant.
Safe Speed Motor (SSM)
Safety Integrated –
Description of functions
(continued)
v
t
SLS
G_D211_XX_00307
t
G_D211_XX_00209
v
1
0