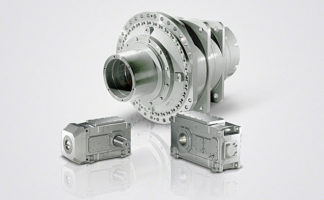
SINAMICS S150 NEMA
Engineering Information
3
Siemens D21.7
(Part 2) – 2015
Option K82 Terminal interface for STO and SS1
Option K82 “Terminal interface for Safety Integrated
functions STO and SS1” provides a convenient customer
interface for enclosed drives (terminal strip X41) that offers:
• 3rd party certification of compliance with the relevant
safety standards
• A wide voltage range for input signals 24 VDC - 230 VAC
• Contact for checkback signal
The operator control element must be a safety switch in
accordance with the relevant standards, or a certified
safety controller.
The circuit can be parameterized for either STO or
SS1 functions:
• STO (immediate blocking of inverter, coast to stop), or
• SS1 (fast ramp down; STO will be activated after a
(parameterized) time delay).
Note that if SS1 is activated when the motor is stationary,
the STO signal making the drive safe will only be activated
after the ramp down delay time. The checkback signal
confirms when STO is effective.
The following information related to external control circuit
wiring is provided as a guideline only. Please refer to the
relevant manuals for current specifications to be used for
circuit design:
Control power 24 VDC to 230 VAC (-15%, +10%); Max. wire
size 2,5 mm²; fuse max. 4 A
Max. wire length (applies to the sum of the outgoing and
return lines):
• AC control voltage, 60 Hz (cable capacitance max.
300 pF/m [91.4 pF/ft]):
– 24 V: 4,000 m [13,100 ft]
– 110 V: 640 m [2,100 ft]
– 230 V: 1600 m [525 ft]
• DC control voltage 24 V (min. cross-section 0.75 mm²/#
xx AWG): 1,500 m [4,900 ft]
Note that exceeding the maximum wire length and
capacitance will cause malfunction of the safety circuit.
What is the difference between options K82 STO/SS1 and
N57 Emergency OFF category 0 respectively N59/N60
Emergency STOP category 1?
STO and Emergency OFF cat. 0 both result in a coast to stop,
and SS1 and Emergency STOP cat. 1 both result in a fast
ramp down with subsequent removal of power. All these
designs incorporate safety relays.
Differences between these options are the standards and
specifications that are being met. Safety Integrated
functions include strict requirements related to design,
wiring, testing and start-up, and associated certification
by qualified personnel at various stages. There are
requirements for redundancy in certain circuits and
components. These requirements apply to components
and circuitry both inside the drive enclosure as well as
outside in the plant.
The requirements met with Emergency OFF/Emergency
STOP are not as extensive.
Safety Integrated – Overview
(continued)
3/19
Emergency Stop compared to Safety Integrated functions