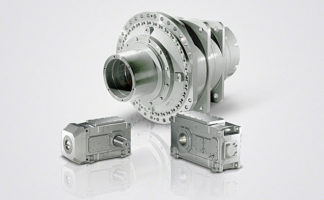
SINAMICS S150 NEMA
Engineering Information
3
Siemens D21.7
(Part 2) – 2015
3/15
SMC30 Sensor Module (options K50 and K52)
Technical data
Design
SMC30 Sensor Module Cabinet-Mounted
Power loss max.
10 W
Encoders which can be
evaluated
• Incremental encoder
TTL/HTL
• SSI encoder with TTL/HTL
incremental signals
• SSI encoder without
incremental signals
• Input impedence
- TTL
570
- HTL, max.
16 mA
• Encoder supply
24 V DC/0.35 A or
5 V DC/0.35 A
• Encoder frequency max.
300 kHz
• SSI baud rate
100 ... 250 kBaud
• Limiting frequency, max.
300 kHz
• Resolution absolute position SSI
30 bit
• Cable length, max.
- TTL encoder
330 ft (100 m) (only bipolar
signals permitted)
1)
- HTL encoder
330 ft (100 m) for unipolar
signals
990 ft (300 m) for bipolar
signals
1)
- SSI encoder
330 ft (100 m)
Conformity
CE
Approvals, according to
cULus
The SMC30 Sensor Module Cabinet-Mounted (options K50
and K52) is required to evaluate the encoder signals of motors
without a DRIVE-CLiQ interface. External encoders can also
be connected via the SMC30.
The following encoder signals can be evaluated:
• Incremental encoders TTL/HTL with/without open-circuit
detection (open-circuit detection is only available with
bipolar signals)
• SSI encoder with TTL/HTL incremental signals
• SSI encoder without incremental signals
The motor temperature can also be detected with KTY84-130
or PTC thermistors.
The SMC30 Sensor Module Cabinet-Mounted features the
following interfaces as standard:
• 1 encoder connection including motor temperature
detection (KTY84-130 or PTC) via SUB-D connector
or terminals
The status of the SMC30 Sensor Module Cabinet-Mounted is
indicated via a multi-color LED.
The maximum encoder cable length between SMC30
modules and encoders is 330 ft (100 m). For HTL encoders,
this length can be increased to 990 ft (300 m) if the A*, A
and B*, B signals are evaluated and the power supply cable
has a minimum cross-section of #20 AWG (0.5 mm
2
).
The signal cable shield can be connected to the SMC30
Sensor Module Cabinet-Mounted via a shield connection
terminal, e.g. Phoenix Contact type SK8 or Weidmüller type
KLBÜ CO 1.
1)
Signal cables twisted in pairs and shielded.
When is a speed feedback encoder recommended?
SINAMICS S150 is capable of accurately controlling torque
at and near zero speed without a speed feedback encoder.
A speed feedback encoder is therefore required only rarely.
A speed feedback encoder should be considered if one
or more of the following applies to the (usually constant
torque) application:
• Maximum speed accuracy
• Very high dynamic performance requirements
• Accurate control of torque below 5% speed (especially
with overhauling loads)
• High starting torque or high overloads at low speeds
(especially with overhauling loads)