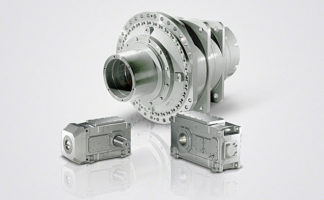
SINAMICS S150 NEMA
Engineering Information
3
Siemens D21.7
(Part 2) – 2015
(3 : Vector) Current fault in
F 07901 Motor overspeed
Help
Alt
Back
Ack.
G_D011_en_00050
G_D011_e
n
_00051
Motor overspeed
Fault val = 000000007
00000007 (hex)
Cause:
The maximum permisible positive or
negative speed has been exceeded.
The maximum permissile positive speed
is calculated as follows:
Back
Motor data
Back
p0304
MOT.U_rated
400.0 V
p0305
MOT. I_rated
405.0 A
p0307
MOT.P_rated
235.0 kW
p0308
MOT.CosPhi_ rated
0.870
Help
Change
OK
G_D011_en_00048
G_D011_en_00049
Basic commissioning
Back
p0700
Pre-assignment BI
S/G150
TM 32
p1000
Default DI n_set
TM 31
AIO
p1080
Minimum speed
0.000
rpm
-1
p1082
Maximum speed
1500.000
rpm
-1
Help
Change
Further
Service / Commissioning
Drive commissioning
Device commissioning
AOP
settings
AOP
diagnosis
Help
G_D011_en_00047
Back
Select.
Operation
12:25:30
Nset
Fout
M
Pact
Nact:
1450.0 rpm
1450.00
48.50
2700
410
rpm
Hz
Nm
kW
1450.0 rpm
385.3 V
748
Nact
Imot
Vout
G_D011_EN_00011b
0%
50
100%
0%
50
100%
G_D011_EN_00012b
Operation
12:25:30
NSET
1465.50
rpm
Pact
410
kW
Fout
48.50
Hz
Vout
385.3
V
Imot
748 A
Nact
1465 rpm
AOP30 advanced operator panel
The advanced operator panel is mounted in the
enclosure door of the drive for operation, monitoring and
commissioning tasks. The AOP30 features a graphical LCD
with backlighting for plain text and bar graph display of
process variables.
The AOP30’s two-stage safety concept prevents unintentional
or unauthorized changes to settings. Operation of the drive
from the operator panel can be disabled by a password
ensuring that only parameter values and process variables
can be displayed on the panel. The OFF key is factory-set to
active but can also be deactivated by the customer. Another
password can be used to prevent the unauthorized
modification of drive parameters.
During the first start-up of the drive, the user will automatically
be guided through the initial start-up procedure that allows a
very simple and quick commissioning process. Only 6 motor
parameters (from the motor nameplate) have to be entered
when the drive is started up for the first time. The control
is then optimized automatically to fine-tune the drive to
the motor.
English, Spanish, French, German, Italian and Chinese
are stored on the CU320-2 Control Unit’s CompactFlash card
as operator panel languages. The desired language must be
downloaded to the AOP30 prior to commissioning. Polish,
Portuguese, Russian and Czech are available in addition to
these standard panel languages. These can be downloaded
free of charge from the Internet under the following link:
The following pictures show screen shots of the display in
various operating phases, beginning with first start-up.
Only 6 motor parameters need to be entered: Output power,
speed, current, power factor, voltage and frequency of
the motor.
3/7
Operator panel
This information can be found on the motor nameplate,
and is entered into the screens on the display by following
a short, menu-driven procedure. The type of motor cooling
must be entered in addition.
The next screen contains the parameter values that are used
to automatically optimize the control.
During operation, current data such as setpoint and actual
values is indicated on the display as absolute values in either
US or international units, or in percent. Up to three process
variables can be viewed as a quasi-analog bar graph.
Any
alarms
which occur are indicated by flashing of the
yellow “ALARM” LED, while
faults
are signaled by a lit red
“FAULT” LED. There is also an indication of the cause
displayed in plain text on the display’s status line.
Alarms and faults are displayed and stored with a time stamp.