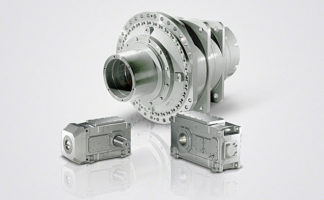
14/6
Siemens D 21.4 · 2017
14
Drive applications
Servo pumps
■
Overview
Servo pump – the energy-saving solution for
hydraulic machines
Outstanding efficiency all along the line
Efficiency is becoming an increasingly important factor in the
optimization of hydraulic machines and plants. This basically
applies to all types of hydraulically driven axis, but particularly
to the axes of presses, injection molding machines and blow
molding machines, for example. In addition to the trend in favor
of hydraulic machines which are partially or fully electrical in
design, it is also beneficial to optimize the hydraulic units them-
selves.
Energy saving made easy
With its new, highly dynamic servo pump, Siemens has the
perfect answer. With energy savings of up to 70 %, your invest-
ment in the future will pay off within a very short time. Suitable
combinations comprising at least one hydraulic pump and a
SIMOTICS synchronous motor - a development which is state of
the art with respect to energy efficiency - will guarantee that you
achieve maximum energy savings.
■
Benefits
The advantages at a glance
•
High energy efficiency: Savings of up to 70 %
•
Active control of the servo pump on the basis of
Drive Control Chart (DCC)
•
Enormous reduction in noise emissions
•
High efficiency
•
Simple drive system with broad scope of functions
•
Reduced complexity
•
Easy system integration
•
Simple preventive maintenance
•
Reduction in quantity of valves
•
Optimum adaptation of force and velocity to the
pressing process
•
Precise reproducibility of velocity, force and cycle rates
•
Small oil tank
•
Highly developed diagnostics capability
•
Modular design
■
Application
Process-optimized use of energy
Energy-efficient, modernized systems generally consume only
as much energy as the hydraulic machines need in the relevant
phases. The energy saving effect is greatest during "idle times":
The servo-driven pump is then virtually at a standstill and
consumes only a minimal amount of energy, by contrast with
the pump in conventional solutions which needed to continue
running at a reduced output (15 to 20 %).
© Siemens AG 2017