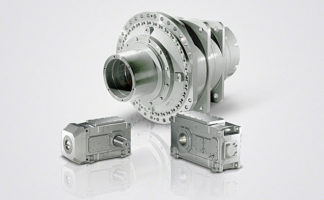
14/5
Siemens D 21.4 · 2017
14
Drive applications
Test stands
■
Overview
Machines for performing reproducible characteristic tests
Test stands are available for many areas. Irrespective whether
an automotive, roller, gearbox, motor, power or some other
component test stand is involved.
In addition to the mechanical design for mounting the test ob-
ject, the drive and control equipment as well as sensors must be
provided to be able to produce the characteristics and record
the measured values.
Test stand requirements
Test stands require a variety of different technological functions,
for example:
•
Consistent speed and torque
•
An open and flexible closed-loop control system with BICO
engineering to provide outstanding torque quality
•
Rotating field frequencies up to 3200 Hz
•
Energy recovery for braking without dangerous current
harmonics with adjustable power factor
•
Resistance to power fluctuations
•
Energy exchange in the coupled DC link for multi-axis test
stands
•
Integration of modern simulation tools, such as Matlab or
Labview
•
Computer link for long-term data recording and a continuous
trace (including ability to export measurements for evaluation
by external tools)
•
Extremely high dynamic response, e.g. for the simulation of
internal combustion engines
•
Integrated safety functions, e.g. SLS on entering the test cell
•
Battery simulation integrated in test stand
•
Setpoint specification in real time by PROFINET IRT or an
internal drive function
These functions can be implemented by combining a
SINAMICS S120 multi-axis converter with SIMOTICS motors.
The SIMOTION control system is a freely programmable
platform for control structures that can be configured and
connected for optimum isochronous operation with PROFINET.
■
Benefits
In addition to supplying the appropriate products, Siemens can
also support you:
•
With the planning of a test stand
•
By conducting extensive vibration calculations:
- Rotor dynamics analyses
- Multi-body simulations
•
With engineering tasks by providing openness for external
setpoint sources (e.g. simulation tools)
•
By supplying extended drive technologies
(e.g. SINAMICS TEC for simulating combustion engines).
■
Design
The solution illustrated in the diagram demonstrates how
combustion engines in the automotive industry are tested "cold"
in the end-of-line area.
Combustion engines are quality-tested directly in the assembly
line. In cold testing as opposed to hot testing, the engine is not
powered by fuel but electrically, which allows for more eco-
friendly testing. On completion of the leak test, the engine is
filled with oil and, if required, with fuel. The cold test results will
show whether the engine complies with quality requirements.
The challenge in this case is to identify any asymmetry or
deviation in relation to a stored reference engine.
■
More information
You can find additional information on the Internet at:
/teststands
3 AC 380 ... 480 V
50 ... 60 Hz
Line Modules
up to 1.2 MW
Motor
Modules up to
800 kW
Common DC
busbar
Test
under
load
Absorber
Braking
resistor
G_D211_EN_00343
DRIVE-CLiQ
SINAMICS S120
Control
Unit
CU320-2
© Siemens AG 2017