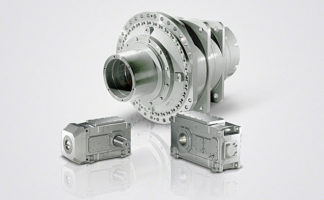
13/43
Siemens D 21.4 · 2017
Tools and configuration
Configuration notes
Mechanical configuration of the drive system
13
■
Configuration
(continued)
Configuration of a drive line-up in chassis format
•
The Motor Modules must be positioned to the left or right of the
Line Module with decreasing rated currents (i.e. the Motor
Module with the highest rated current is positioned next to the
Line Module, while the Motor Module with the lowest rated
current is at the end on the left or right). You must ensure that
the cables/busbars for the DC link meet the current-carrying
capacity requirements for all connected Motor Modules.
•
The inductance of the DC link busbars must be low, achieved,
for example, by arranging the bars as close as possible in
parallel, but observing the required creepage distances and
air gaps.
•
The Control Unit configuration is flexible. The following
configuration options are possible:
- "Docking" on the left-hand side of the Line Module
-
Direct mounting next to the drive line-up on a mounting plate
- Mounting in other cabinet panels taking into account the
permissible DRIVE-CLiQ cable lengths
Configuration of a mixed drive line-up in chassis and
booksize formats
A mixed drive line-up must be configured according to the rules
for chassis format units. The Motor Modules in booksize format
can be connected to the higher-level DC link busbars by means
of DC link rectifier adapters. There are two possible connection
options - A and B. With A, each Motor Module in booksize format
is connected using the appropriate DC link rectifier adapter. With
B, Motor Modules in booksize format are connected to one
another and the internal DC link busbars and a DC link rectifier
adapter are used on the last Motor Module to make the connec-
tion to the higher-level DC link busbars. In the latter case, the DC
link rectifier adapter must be attached to the last Motor Module
on the right-hand side of the line. As regards the arrangement of
modules with different current ratings, the guidelines specified
under "Configuration of a drive line-up in booksize format" also
apply to mixed drive line-ups.
Ideally, the entire length of the higher-level DC link busbars can
be dimensioned for the rated DC link current of the Line Module.
The busbars are then protected by the line fuses at the infeed
end.
If the cross section of the DC link busbars or cabling is reduced,
this branch must be designed to be short-circuit-proof. The cur-
rent limiting mechanism of the Motor Modules connected to the
branch with reduced cross section then protects it against over-
loading. It is not advisable to reduce busbars or cables down to
the mandatory minimum cross section. No additional overload
protection (fuse) is required on the assumption that overloading
cannot occur as a result of cable damage on the cable route to
the Motor Module and that the circuit branch is protected against
overloading by the Motor Module.
Where the cross section has been significantly reduced, or the
circuit design is not inherently short-circuit-proof, a branch fuse
must be installed at the beginning of the section with reduced
cross section in order to protect the DC link connections in-
volved. In the event of a fault, the fuse must be capable of inter-
rupting DC fault currents; other types of miniature circuit breaker
are not suitable.
Allocation of branch fuses for option (A) in a supply system with
grounded neutral (TN system). The calculations are based on
the assumption that
τ
=
L/R
<
10 ms applies to the time constant
τ
in the DC fault circuit and that the fault current is interrupted by
the fuse after maximum 1 s.
Motor
Module
Motor
Module
Active
Interface
Module
Motor
Module
Motor
Module
Motor
Module
Active
Line
Module
high
power
low
power
high
power
low
power
DC interface
G_D211_EN_00022a
A
B
high
power
low
power
low
power
high
power
G_D211_EN_00134a
Motor
Module
Motor
Module
Motor
Module
Motor
Modules
Motor
Module
Motor
Module
Active
Interface
Module
Active
Line
Module
© Siemens AG 2017