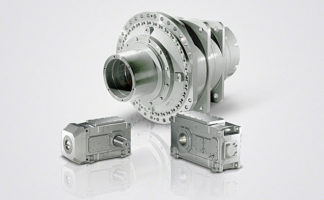
13/42
Siemens D 21.4 · 2017
Tools and configuration
Configuration notes
Mechanical configuration of the drive system
13
■
Configuration
Specification of components for connection system
To complete the drive system, components such as motors and
encoders must be connected to it via cables.
For motors with DRIVE-CLiQ interface, the DRIVE-CLiQ cables
carry the 24 V DC power supply. On all other Sensor Modules, a
separate 24 V DC power supply must be provided.
Drive connection system
DRIVE-CLiQ cables are available in different versions and
lengths
(see section MOTION-CONNECT connection systems)
.
The required bending radii apply particularly to short cables.
In addition to the distance between the two DRIVE-CLiQ sockets
that the cable is to connect, a cable length of at least 60 mm
(2.36 in) must be added to allow for bending radii.
When
defining lengths of prefabricated cables, see section
MOTION-CONNECT connection systems.
Unused DRIVE-CLiQ sockets can be sealed with a blanking plug
to prevent the ingress of contaminants. Suitable blanking plugs
are supplied in the accessories pack for the units.
Mechanical configuration of the drive
A SINAMICS S drive line-up comprises a Line Module, Motor
Modules, DC link components, a Control Unit, and the optional
expansion modules.
Configuration of a drive line-up in booksize format
The following criteria must be taken into account when a drive
line-up of booksize format units is configured:
•
The Smart Line Modules 5 kW and 10 kW must always be
arranged on the left as the first module. All other Line Modules
should be arranged on the left as the first module. The
CU320-2 Control Unit in this case can be "snapped onto"
the left-hand side of the Line Module.
•
The DC link busbars can be connected on the right and left
with Basic Line Modules, Active Line Modules and Smart Line
Modules rated 16
kW and larger. In this case, the modules can
be arranged in reverse order (from right to left) or on both
sides
(see arrangement for units in chassis format)
.
•
Only one Line Module is permitted in each drive line-up.
•
A number of drive line-ups must be configured for power
supplies which cannot be provided by the highest rating.
•
The Motor Modules must be arranged beside the Line Module
in descending order of the rated currents, that is, the Motor
Module with the highest rated current is to be mounted
immediately adjacent to the Line Module, and the Motor
Module with the lowest rated current is positioned furthest
away from the Line Module.
•
DC link busbars are integrated in the Line Modules, Motor
Modules, Braking Modules, Capacitor Modules and Control
Supply Modules so that the modules can be connected to the
drive line-up. The current carrying capacity of the integrated
DC link busbars is determined by the module rating and is
either 100
A or 200 A
(see technical specifications)
. It must be
ensured that the DC link busbars have the required current
carrying capacity at every point within the drive line-up. When
high-output Motor Modules (DC link busbars 200 A) and low-
output Motor Modules (DC link busbars 100 A) are used, for
example, the Braking Module (DC link busbars 100 A) must
be installed downstream of the high-output Motor Modules.
•
DC link adapters can be used to implement multi-tier
configurations.
•
The drive line-ups should be configured such that the total
length of all power cables for the motor cables and the line
cable, which should preferably be shielded, in each individual
line-up does not exceed the permissible total cable length.
Power-oriented arrangement of booksize format Motor Modules
•
The Control Unit configuration is flexible. The following
configuration options are possible:
- "Docking" on the left-hand side of the Line Module
-
Direct mounting next to the drive line-up on a mounting plate
- Mounting in other cabinet panels taking into account the
permissible DRIVE-CLiQ cable lengths
Legend
Cable
Description
(1)
DRIVE-CLiQ cables
Standard cables for cabinet-internal
configuration without 24 V cores
(2)
DRIVE-CLiQ
MOTION-CONNECT
500/800 cables
Shielded cables with 24 V cores
MOTION-CONNECT 500 for fixed
installation (e.g. in a cable channel)
and MOTION-CONNECT 800 for
flexible installation (e.g. in cable
carriers)
(3)
MOTION-CONNECT
500/800 signal cables
Suitable for the relevant measuring
system; in versions
MOTION-CONNECT 500 for fixed
installation (e.g. in a cable channel)
and MOTION-CONNECT 800 for
flexible installation (e.g. in cable
carriers)
(4)
MOTION-CONNECT
500/800 power cables
Shielded motor cables
MOTION-CONNECT 500 for fixed
installation (e.g. in a cable channel)
and MOTION-CONNECT 800 for
flexible installation (e.g. in cable
carriers)
TM31
CU
320-2
SMC
(1)
(4)
(2)
(3)
(1)
Motor with
DRIVE-CLiQ
interface
Line
Module
Motor
Module
Motor
Module
G_D212_EN_00016c
high
power
low
power
G_D211_EN_00136a
Line
Module
Motor Modules
Braking
Module
Capacitor
Module
Control
Supply
Module
© Siemens AG 2017