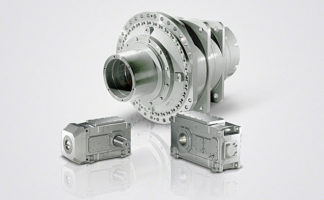
13/38
Siemens D 21.4 · 2017
Tools and configuration
Configuration notes
System components
13
■
Configuration
Motor reactors
High-speed switching of the power transistors causes capaci-
tive recharging currents in the motor cable and motor, as well as
steep voltage rises and peak voltages in the motor windings.
These currents can be reduced by installing a motor reactor.
The voltage drop across the motor reactor is normally negligible
at output frequencies of 60 Hz and below. The per unit voltage
drop
u
k
across the reactor is between 1 % and 4 % at rated cur-
rent and 50 Hz. With a cos
ϕ
of 0.86 and an output frequency of
50 Hz, the motor voltage is about 2 % lower (as a result of the
motor reactor) than in systems without a motor reactor.
Phasor diagram of motor with motor reactor
Motor reactors are compatible with all modulation types
(space vector modulation, edge modulation).
Sine-wave filters
Sine-wave filters are low-pass LC filters which only let through
the fundamental component of the square-wave, pulse-width-
modulation output voltage of a Power Module or Motor Module.
The resonant frequency of the sine-wave filter must be signifi-
cantly lower than the pulse frequency of the Power Module or
Motor Module and be dimensioned with a sufficient margin to the
maximum permissible output frequency. Sine-wave filters there-
fore define the choice of pulse frequency and place a limit on the
maximum possible output frequency. This type of filter is com-
patible only with space vector modulation. The output voltage of
a Power Module or Motor Module is thus limited to an output volt-
age (rms value) of approximately 0.67 x DC link voltage. With the
voltage drop across the sine-wave filter, the maximum possible
output voltage (rms value) is approximately 0.63 x DC link volt-
age. Parameters are used to register a sine-wave filter with the
Control Unit. This ensures that all those values that are depen-
dent on it, such as permissible modulation modes and maximum
output frequency, are correctly preassigned.
Sine-wave filters can be used only in conjunction with Vector
Control and V/f Control modes.
dv/dt filter plus VPL and dv/dt filter compact plus VPL
The dv/dt filter plus VPL and dv/dt filter compact plus VPL com-
prise two components, i.e. a dv/dt reactor and a voltage limiting
network (Voltage Peak Limiter). As a consequence, the use of
dv/dt filters plus VPL and dv/dt filters compact plus VPL rep-
resents a suitable method of reducing the voltage load on the
motor winding for line supply voltages of 500 V to 690 V to such
an extent that a special motor insulation is not required. The
bearing currents are also significantly reduced. Using these
filters therefore allows standard motors with standard insulation
and without insulated bearings to be operated with SINAMICS
converters up to line supply voltages of 690 V. This applies to
both Siemens motors and third-party motors.
Sensor Modules
Signal conditioning for various encoders (incremental encoder
sin/cos 1 V
pp
, absolute encoder, resolver) takes place remotely,
i.e. in the vicinity of the encoder, with customized Sensor
Modules. Depending on the measuring system, SMC10, SMC20
or SMC30 Sensor Modules are used. The Sensor Modules are
designed to be mounted on DIN rails. They are also used for the
signal conditioning of external (machine) encoders.
Expansion modules
The CU320-2 Control Unit features interfaces and terminals for
communication as standard. SINAMICS S120 offers the
following expansion modules:
•
TB30 Terminal Board (terminal expansion for plugging into the
option slot on the CU320-2 Control Unit)
•
TM31 Terminal Module (terminal expansion for connection via
DRIVE-CLiQ)
The following criteria regarding the use of expansion modules
must be taken into account:
•
Only one option board can be plugged into the option slot on
the CU320-2 Control Unit.
•
A maximum of 8 Terminal Modules may be operated in a drive
line-up.
Braking Modules and braking resistors
Braking units comprise a Braking Module and a braking resistor,
which must be attached externally.
Braking units are used when
•
regenerative energy occurs occasionally and briefly, for
example when the drive brakes (EMERGENCY STOP) and the
drive has no regenerative feedback capability
•
the drive features regenerative feedback units but cannot
return the energy fast enough to the supply on an
"EMERGENCY STOP"
•
the drive needs to be shut down after a power failure
The braking units for Power Modules in blocksize format consist
of braking resistors only, as they feature a Braking Module as
standard.
A number of Braking Modules can be connected in parallel to
the DC link in order to increase the braking power. Each Braking
Module requires its own braking resistor. It is not permissible to
operate a mix of braking units in booksize and chassis format on
the same DC link.
The braking power required is calculated from the DC link power
P
d
of the drive line-up or Power Module in generator operation.
Motor reactor
U
G_D211_EN_00131
Motor
U
a
U
90°+
a
© Siemens AG 2017