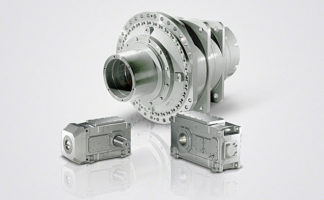
13/34
Siemens D 21.4 · 2017
Tools and configuration
Configuration notes
Power units
13
■
Configuration
(continued)
The following factors must also be taken into account when
dimensioning the DC link:
Braking operation
As device losses are important in motor mode, the dimensioning
for motor mode is also applicable to generator mode. With re-
spect to motor braking operation, check that the energy fed
back into the DC link does not exceed the permissible peak load
capability of the Line Module.
In the case of higher regenerative outputs and to control the "line
failure" operating scenario, a Braking Module must be provided,
the Smart or Active Line Module must be overdimensioned or the
regenerative output reduced by longer braking times.
For the configuration of the "EMERGENCY STOP" operating sce-
nario, the Line Module must either be overdimensioned or an ad-
ditional Braking Module must be used, so that the DC link energy
can be dissipated as quickly as possible.
Checking the DC link capacitance
During power-up, the Line Modules limit the charging current for
the DC link capacitors. Due to the limits imposed by the pre-
charging circuit, it is essential to observe the maximum permis-
sible DC link capacitance values for the drive line-up specified
in the technical specifications.
Frequency with which the DC link is precharged
For chassis format Line Modules, the maximum permissible DC
link pre-charging interval is 3 minutes.
Parallel connection of power units
Up to 4 Motor Modules or Line Modules in chassis format can be
connected in parallel. Parallel connections can operate only in
the Vector Control mode.
Parallel connections may only include Motor Modules or Line
Modules of the same type and with the same voltage and output
ratings. Mixtures of different modules, e.g. Basic Line Modules
and Active Line Modules, cannot be connected in parallel. The
CU320-2, SIMOTION D4x5-2 or CX32-2 Control Unit can control
only one drive object of type "Parallel connection Line Modules"
and one of type "Parallel connection Motor Modules". It is as-
sumed that all Line Modules or Motor Modules linked to the Con-
trol Unit are connected in parallel. A Control Unit can control, for
example, the following components:
•
1 Line Module + 2 parallel-connected Motor Modules
•
2 parallel-connected Line Modules + 3 parallel-connected
Motor Modules
Combinations such as the following are not permissible:
2 Line Modules + 2 parallel-connected Motor Modules +
1 Motor Module
Further information can be found in the following Engineering
Manual:
System disturbances
The voltage drops across the impedance between the supply
system and a load as soon as the load draws current. In a sym-
metrical three-phase supply system, this is the network imped-
ance
Z
n
which is calculated from the impedance
Z
s
of the supply
system and the line-side impedance
Z
e
of the load.
Effective impedances when a load is connected to a three-phase supply
system
Z
n
=
Z
s
+
Z
e
=
R
s
+ j
X
s
+
R
e
+ j
X
e
=
R
n
+ j
X
n
On a variable-speed drive, the line-side impedance
Z
e
is normally
the total impedance provided by the line reactor and the feeder
cable up to the PCC (Point of Common Coupling) for further loads.
The ohmic component
R
n
is generally negligible as compared to
the inductive component
X
n
. The inductance of an RI suppression
filter is irrelevant for the purpose of this calculation, as this induc-
tance is effective only for asymmetrical interference voltages, but
not for a symmetrical line current.
If a load causes voltage drops across the impedance
Z
s
, this
system disturbance has an impact at the PCC and thus also in
the supply voltage to all other loads.
The voltage drop is proportional to current
I
e
and the impedance.
To facilitate comparison of voltage drops under different supply
and load conditions, the voltage drop is specified – normally at
rated current – with reference to the phase voltage
U
o
. The calcu-
lation formula, e.g. for the per unit voltage drop
u
k
across an im-
pedance
Z
is as follows:
u
k
=
Z
×
I
e
/
U
o
G_D211_EN_00126
rated
V
N
Z
s
e
e
e
e
s
s
0
other loads
Z
Z
X
R
X
R
U
PCC
W1
V1
U1
Load
© Siemens AG 2017