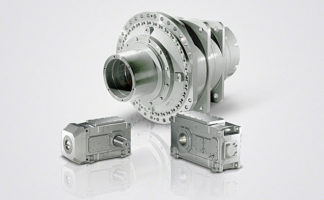
13/33
Siemens D 21.4 · 2017
Tools and configuration
Configuration notes
Power units
13
■
Configuration
(continued)
Line Modules
In multi-axis drive applications, a number of Motor Modules are
operated on a common DC link, which is supplied with power by
a Line Module.
The first task is to decide whether a Basic Line Module, Smart
Line Module or an Active Line Module will be used. On one hand,
this depends on whether the drive must be capable of regener-
ative feedback into the line supply and, on the other hand,
whether the line infeed is uncontrolled, and therefore dependent
on the line supply voltage, or controlled to obtain a constant DC
link voltage. For an uncontrolled infeed Basic Line Modules/
Smart Line Modules, line voltage changes can influence the
output power of the Line Modules.
The chassis format units are available in the 380 V to 480 V volt-
age range, but also include units in the 500 V to 690 V range.
Basic Line Modules are designed for infeed operation only.
Active Line Modules have regulated infeeds which feature a
step-up function.
In order to calculate the required DC link power and select the
correct Line Module, it is important to analyse the entire oper-
ating sequence of the drive line-up connected to the DC link.
Factors such as partial load, redundancies, duty cycles, coinci-
dence factors and the operating mode (motor / generator mode)
must be taken into account.
The DC link power
P
d
of a single Motor Module is calculated from
the shaft output
P
mech
of the motor and the efficiency of the
motor
η
m
and Motor Module
η
wr
.
The following applies in motor mode:
P
d
=
P
mech
/ (
η
m
×
η
wr
)
The following applies in generator mode:
P
d
=
P
mech
×
η
m
×
η
wr
The motor and generator outputs must be added with the
corresponding sign in order to calculate the total DC link power.
For the power calculation, the DC link voltage
U
d
can be as-
sumed to be constant. Therefore, the required DC link current
can be calculated as
I
d
=
P
d
/
U
d
Basic Line Modules
The DC link voltage
U
d
of the Basic Line Modules is load-depen-
dent. Under no-load conditions, the DC link is charged to the line
voltage crest value
U
L
, i.e.
U
d
=
√
2 ×
U
L
, e.g.
U
d
= 566 V when
a 400 V supply system is connected.
Under load conditions, the DC link voltage reaches the average
value of the rectified line voltage applied to the terminals. This
mean value results from the line voltage times a factor of 1.35.
Under full load, the voltage in the DC link is slightly less than the
theoretical value due to the voltage drop across the line reactor
and the line feeder cable. In practice, the range of the DC link
voltage
U
d
is as follows:
1.41 ×
U
L
>
U
d
> 1.32 ×
U
L
(no load
→
rated power)
Smart Line Modules
The DC link voltage
U
d
of Smart Line Modules is regulated to the
average value of the rectified line voltage
U
L
, i.e.
U
d
≈
1.35 ×
U
L
Due to the voltage drop across the line reactor and in the line
feeder cable, the DC link voltage decreases in motor operation
and increases in generator operation. The DC link voltage
U
d
thus varies within the same range as on drives with a Basic
Line Module:
1.41 ×
U
L
>
U
d
> 1.32 ×
U
L
(rated power, generating
→
rated power, motoring)
Active Line Modules
The DC link voltage
U
d
is regulated to an adjustable value
(Active Mode). An Active Line Module can also be switched to
Smart Mode and then operates like a Smart Line Module. In
Active Mode, the Active Line Module draws a virtually sinusoidal
current from the supply system.
The rated infeed power of the Line Module refers to a line voltage
of 380 V, 400 V or 690 V (690 V applies only to chassis format
Line Modules).
Depending on the ambient conditions (installation altitude, am-
bient temperature), the rated infeed power of the Line Modules
may need to be reduced
(see section SINAMICS S120 drive
system)
.
The coincidence factor takes into account the time characteristic
of the torque for each individual axis.
On the basis of these principles, the following procedure can be
used to dimension the Line Module:
Required DC link power determined for each
axis (taking into account the speed ratio, if
required)
Axes categorized
according to output class
Simultaneity factor used for each output
class and the required DC link power
determined for each output class
Total required DC link power determined
Selection of Line Module taking into
account the supply voltage and ambient
conditions
G_D212_EN_00012
© Siemens AG 2017