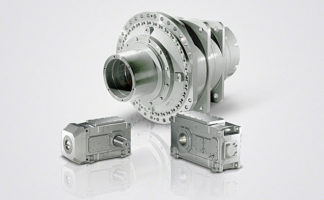
13/31
Siemens D 21.4 · 2017
Tools and configuration
Configuration notes
Power units
13
■
Configuration
(continued)
Selection of the Power Module or Motor Module
The Motor Module is selected initially on the basis of standstill
current
I
0 100 K
(rated current for winding temperature rise 100 K)
for synchronous motors and the rated current
I
rated
for asynchro-
nous motors (induction motors), and is specified in the motor
description. Dynamic overloads, e.g. during acceleration, must
be taken into account by duty cycles and may demand a more
powerful Power Module or Motor Module. In this context, it is also
important to remember that the output current of the Power
Module or Motor Module decreases as a function of installation
altitude, ambient temperature and pulse frequency setting
(see
explanations of derating characteristics)
.
For an optimum configuration, the rms motor current
I
load
calcu-
lated from the duty cycle is replicated on the Power Module or
Motor Module. The following must apply:
I
rated, module
≥
I
load
I
rated, module
= permissible continuous current of Power Module
or Motor Module taking derating characteristic curves into
account
The Power Modules or Motor Modules can be required to supply
a higher output current for specific time periods. The character-
istics or overload capability must be noted
(see section
SINAMICS S120 drive system)
when modules are engineered
for overload.
The SIZER for Siemens Drives engineering tool is capable of
performing precise overload calculations.
Rated current – permissible and non-permissible
motor/converter combinations
•
Motor rated current higher than rated output current of the
Power Module or Motor Module:
In cases where a motor with a higher rated current than the
rated output current of the Power Module or Motor Module is
to be connected, the motor will only be able to operate under
partial load. The following limit applies:
The short-time current (= 1.5 × base-load current
I
H
) should
be higher or equal to the rated current of the connected motor.
Adhering to this dimensioning rule is important because the
low leakage inductance of large motors causes current peaks
which may result in drive system shutdown or in continuous
output limiting by the internal protective electronic circuitry.
•
Motor rated current significantly lower than rated output
current of the Power Module or Motor Module:
With the vector control system used, the rated motor current
must equal at least 1/8 of the rated output current of the Power
Module or Motor Module. With lower motor currents, the drive
can be operated in V/f control mode.
Using pulse width modulation, the Power Modules or Motor
Modules generate an AC voltage to feed the connected motor
from the DC voltage of the DC link. The magnitude of the DC link
voltage is determined by the line voltage and, in the case of a
Motor Module, by the Line Module used and thus the maximum
possible output voltage
(see section SINAMICS S120 drive
system).
The speed and loading of the connected motor define
the required motor voltage. The maximum possible output volt-
age must be greater than or equal to the required motor voltage;
it may be necessary to select a motor with a different winding.
It is not possible to utilize all modes of pulse width modulation
when a sine-wave filter is connected. The maximum possible
output voltage
(see sine-wave filter)
is lower as a result.
© Siemens AG 2017