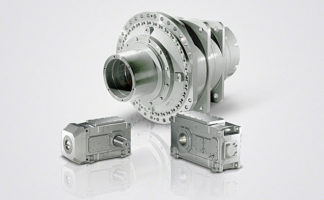
13/29
Siemens D 21.4 · 2017
Tools and configuration
Configuration notes
Power units
13
■
Configuration
Overload capability
The power units of the Line Modules, Motor Modules and Power
Modules are designed for brief overloads, i.e. the Modules are
capable of supplying more than the rated current
I
rated
for short
periods. In this instance, the thermal capacity of the heat sink is
utilized, allowing for the relevant thermal time constants. The
power semiconductors and actual current sensing circuit are
rated for a maximum current
I
max
which must not be exceeded.
The overload capability is determined by
I
max
,
I
rated
and the ther-
mal time constants. A number of characteristic duty cycles are
defined in the technical specifications for the power units. The
SIZER for Siemens Drives engineering tool calculates the load
on the basis of a specified duty cycle with optional time charac-
teristic and then identifies the power unit which is required.
The thermal time constant of a power semiconductor chip is
typically within the range of 100 ms. With frequencies below
10 Hz, the overload capacity is therefore limited. The software
takes account of these limitations by means of a thermal model
and protects the devices against overload in all operating states.
It must be noted, especially at frequencies around 0 Hz, that the
specified rated current
I
rated
is the root-mean-square value of a
sinusoidal current. If the frequency of the three-phase system is
reduced to 0 Hz, a pure direct current flows in all phases at
standstill. The root-mean-square value of this direct current can
reach the peak value of the sinusoidal current depending on the
phase relation.
The output current in this state is greater than the rated current
I
rated
by a factor of
√
2. The individual motor terminals and cables
are designed thermically for the rated current in normal opera-
tion, so the devices are protected against this overload while
taking account of the thermal time constant.
Derating characteristics
The power units can be operated with their rated current or
power and the specified pulse frequency up to an ambient tem-
perature of 40 °C (104 °F). The heat sink reaches the maximum
permissible temperature at this operating point. If the ambient
temperature increases above 40 °C (104 °F), the resulting heat
loss must be reduced to prevent the heat sink from overheating.
At a given current, the heat loss increases in proportion to the
pulse frequency. The rated output current
I
rated
must be reduced
to ensure that the maximum heat loss or heat sink temperature
for higher pulse frequencies is not exceeded. When the correc-
tion factor
k
f
for the pulse frequency is applied, the rated output
current
I
ratedf
that is valid for the selected pulse frequency is
adjusted.
When configuring a drive, please note that power units may not
be capable of supplying the full current or power in the tempera-
ture range between 40 °C (104 °F) and 55 °C (131 °F). The
power units measure the heat sink temperature and protect
themselves against thermal overloading at temperatures
> 40 °C (104 °F).
The air pressure, and therefore air density, drops at altitudes
above sea level. At these altitudes, the same quantity of air does
not have the same cooling effect and the air gap between two
electrical conductors can only insulate a lower voltage. Typical
air pressure values are:
0 m (0 ft) above sea level: 100 kPa
2000 m (6562 ft) above sea level: 80 kPa
3000 m (9843 ft) above sea level: 70 kPa
4000 m (13124 ft) above sea level: 62 kPa
5000 m (16405 ft) above sea level: 54 kPa
At installation altitudes above 2000 m (6562 ft), the line voltage
must not exceed certain limits to ensure that surge voltages can
be insulated in accordance with EN 60664-1 for surge voltage
category III. If the line voltage is higher than this limit at installa-
tion altitudes > 2000 m (6562 ft), measures must be taken to re-
duce transient category III surge voltages to category II values,
e.g. equipment must be supplied via an isolating transformer.
In order to calculate the permissible output current or power, the
derating factors must be multiplied for the effects described
above. The derating factor
k
I
for current as a function of installa-
tion altitude can be offset against the derating factor
k
T
for am-
bient temperature. If the result of multiplying derating factor
k
T
by derating factor
k
I
is greater than 1, then the calculation must
be based on a rated current of
I
rated
or
I
ratedf
. If the result is < 1,
then it must be multiplied by the rated current
I
rated
or
I
ratedf
to
calculate the maximum permissible continuous current. The de-
rating factor
k
=
k
f
×
k
T
×
k
I
calculated by this method to obtain
the total derating value must be applied to all current values in
the specified duty cycles (
I
rated
,
I
H
,
I
L
).
The derating characteristic curves of Power Modules, Line
Modules and Motor Modules can be found in the technical
specifications of the relevant modules
(see section
SINAMICS S120 drive system)
.
I
T
t
t
I
rated
J av
T
J
T
average junction temperature of the power semiconductor
T
junction temperature of the power semiconductor
J av
J
G_D211_EN_00120
0
I
n
√
2 x
I
n
t
G_D211_XX_00219
© Siemens AG 2017