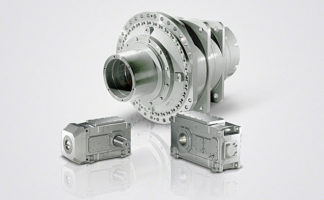
13/26
Siemens D 21.4 · 2017
Tools and configuration
Configuration notes
SINAMICS S120 Control Units
13
■
Configuration
(continued)
Core topologies: Component cabling with DRIVE-CLiQ
The components communicate with one another via the
standard DRIVE-CLiQ interface.
This couples a Control Unit with the power components,
encoders and additional system components, for example
Terminal Modules. Setpoints and actual values, control
commands, status messages and rating plate data of the
components is transferred via DRIVE-CLiQ.
Basic rules for wiring with DRIVE-CLiQ
The following rules apply when wiring components with
DRIVE-CLiQ:
•
A maximum of 14 nodes can be connected to a DRIVE-CLiQ
socket on the CU320-2 Control Unit
•
Up to 8 nodes can be connected in a line. A line is always
seen from the perspective of the Control Unit
•
A maximum of 6 Motor Modules can be operated in a line
•
Ring wiring is not permitted
•
Components must not be double-wired
•
The motor encoder should be connected to the associated
Motor Module
•
Up to 9 encoders can be operated on one Control Unit
•
A maximum of 8 Terminal Modules can be connected
•
It is not permissible for the TM54F Terminal Module to be
operated on the same DRIVE-CLiQ line as Motor Modules
•
The Terminal Modules TM15, TM17 High Feature and TM41
have faster sampling cycles than the TM31 and TM54F. For
this reason, the two groups of Terminal Modules must be
connected in separate DRIVE-CLiQ lines.
•
A DRIVE-CLiQ Hub DMC20/DME20 counts as two nodes
DRIVE-CLiQ configuration examples
There is a basic clock cycle within a DRIVE-CLiQ connection.
For this reason, only combinations of modules with the same
sampling cycle or integer-divisible sampling times can be
operated on a DRIVE-CLiQ connection. To simplify the confi-
guring process, it is advisable to supply the Line Module and
Motor Modules via separate DRIVE-CLiQ connections.
The power components are supplied with the required
DRIVE-CLiQ connecting cable for connection to the adjacent
DRIVE-CLiQ node in the axis grouping (line topology). Pre-
fabricated DRIVE-CLiQ cables in various lengths up to 100 m
(328 ft) are available for connecting motor encoders, direct
measuring encoders, Terminal Modules, etc.
The DRIVE-CLiQ cable connections inside the control cabinet
must not exceed 70 m (230 ft) in length, e.g. connection be-
tween the CU320-2 Control Unit and the first Motor Module or
between Motor Modules. The maximum permissible length of
DRIVE-CLiQ MOTION-CONNECT cables to external compo-
nents is 100 m (328 ft).
Example of a line topology for standard solutions
Example of a tree topology for high-performance solutions, e.g. high-
speed axes in direct motion control group, selective access to individual
axes/axis groupings for maintenance activities, etc.
CU320-2
12
X 103
X 102
X 101
X 100
1
2
3
4
6
7
14
8
9
10
11
5
13
No ring wiring
No double wiring
G_D212_EN_00013b
TM31
TM31
SMC
CU
320-2
SMC
External
measuring
system
Motor with
DRIVE-CLiQ
interface
G_D212_EN_00014b
Line
Module
Motor
Module
Motor
Module
TM31
TM31
SMC
CU
320-2
SMC
External
measuring system
Motor with
DRIVE-CLiQ
interface
G_D212_EN_00015b
Line
Module
Motor
Module
Motor
Module
© Siemens AG 2017