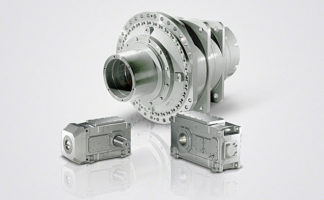
13/17
Siemens D 21.4 · 2017
Tools and configuration
Configuration notes
SINAMICS S120 Control Units
13
■
Overview
For the closed-loop control of drives and the implementation of
basic technological tasks, for SINAMICS S120 the CU320-2
Control Unit is available for multi-axis applications, and the
CU310-2 Control Unit is available for individual drives.
Sophisticated Motion Control tasks are best supported using the
powerful SIMOTION D Control Units (D410-2, D425-2, D435-2,
D445-2, D455-2) with scaled performance.
Each of these Control Units is based on object-orientated
SINAMICS S120 standard firmware, which includes all of the
usual V/f control modes, scalable so that even the highest
performance requirements can be satisfied.
The following are ready-to-configure drive objects (drive controls):
•
The control for a line infeed:
Infeed Control
•
The control for the broad scope of rugged asynchronous
(induction) motors and torque motors, including sensorless:
Vector Control
•
The control for permanent-magnet excited synchronous and
servo asynchronous motors with demanding dynamic require-
ments:
Servo Control
All these control versions are based on the principle of field-
oriented, closed-loop vector control, with a special expansion for
reluctance motors.
The most commonly used V/f control modes are stored in the
"Vector control" drive object and are ideal for implementing even
simple applications such as group drives with SIEMOSYN
motors.
■
Configuration
Guide to selecting a closed-loop control variant
SINAMICS S closed-loop control properties
Criteria for
assessing
control quality
Explanations, definitions
Rise time
The rise time is the period which elapses between an
abrupt change in a setpoint and the moment the actual
value first reaches the tolerance band (2 %) around the
setpoint.
The dead time is the period which elapses between the
abrupt change in the setpoint and the moment the actual
value begins to increase. The dead time is partially deter-
mined by the read-in, processing and output cycles of the
digital closed-loop control. Where the dead time consti-
tutes a significant proportion of the rise time, it must be
separately identified.
Characteristic
angular
frequency
-3 dB
The limit frequency is a measure of the dynamic response
of a closed-loop control. A pure sinusoidal setpoint is
input to calculate the limit frequency; no part of the control
loop must reach the limit. The actual value is measured
under steady-state conditions and the ratio between the
amplitudes of actual value and setpoint is recorded.
-3 dB limit frequency: Frequency at which the absolute
value of the actual value drops by 3 dB (to 71 %) for the
first time. The closed-loop control can manage frequen-
cies up to this value and remain stable.
Ripple
The ripple is the undesirable characteristic of the actual
value which is superimposed on the mean value (useful
signal). Oscillating torque is another term used in relation
to torque. Typical oscillating torques are caused by cer-
tain motor slot arrangements, by limited encoder resolu-
tion or by the limited resolution of the voltage control of the
IGBT power unit. The torque ripple is also reflected in the
speed ripple as being indirectly proportional to the mass
inertia of the drive.
Accuracy
The accuracy defines the magnitude of the average,
repeatable deviation between the actual value and setpoint
under rated operating conditions. Deviations between the
actual value and setpoint are caused by internal inaccura-
cies in the measuring and control systems. External influ-
encing factors, such as temperature or speed, are not
included in the accuracy assessment. The closed-loop and
open-loop controls should be optimized with respect to the
relevant variable.
© Siemens AG 2017