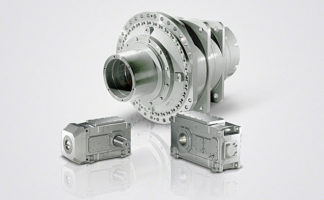
13/12
Siemens D 21.4 · 2017
Tools and configuration
Configuration notes
Planning
13
■
Overview
General configuration sequence
The function description of the machine provides the basis for
the configuration. The definition of the components is based on
physical dependencies and is usually carried out as follows:
Configuration begins with the mechanical interface to the ma-
chine. A suitable motor is selected according to the specified
torques and speeds. A matching power unit is then also chosen.
Depending on the requirements of the machine, the motor is
supplied as a single drive via a Power Module or within a multi-
motor drive group via a Motor Module. Once the basic compo-
nents have been defined, the system components for matching
to the electrical and mechanical interfaces are selected.
The SIZER for Siemens Drives engineering tool allows the cor-
rect components to be selected quickly and easily. Based on the
torque and speed characteristics entered, SIZER for Siemens
Drives guides the user through the configuring process, identi-
fying suitable motors and matching SINAMICS power units and
other system components.
The following sections describe those SINAMICS S120 compo-
nents which are needed to create a drive system subject to
certain boundary conditions. For information about individual
components, please also refer to the online help of the SIZER for
Siemens Drives engineering tool.
Step
Description of configuration activity
1
Clarification of type of drive
2
Definition of boundary conditions and integration into
automated system
3
Definition of loading case, calculation of max. load torque,
definition of motor
4
Definition of the Motor Module
5
Repetition of steps 3 and 4 for additional axes
6
Calculation of the required infeed power and defining the
Line Module
7
Specification of the required control performance and
selection of the Control Unit, definition of component
cabling
8
Specification of the line-side power options (main switch,
fuses, line filters, etc.) and cable cross-sections for
connecting to the line supply and motor
9
Definition of additional system components
10
Calculation of the current requirement for the 24 V DC
supply for the components and specification of power
supplies (SITOP devices, Control Supply Modules)
11
Specification of components for connection system
12
Configuration of drive line-up components
13
Thermal design of the control cabinet
© Siemens AG 2017