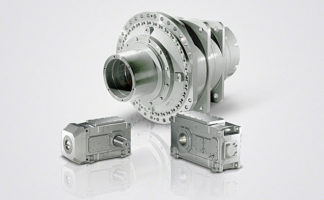
11/4
Siemens D 21.4 · 2017
Motion Control Encoder measuring systems
Built-on optoelectronic rotary encoders
Incremental encoders
11
■
Function
Incremental encoder with sin/cos 1 V
pp
and clamp flange incl. cable with
connector as well as incremental encoder with RS422/HTL and Synchro
flange
Incremental encoders detect relative movement and deliver a
defined number of electrical pulses per revolution, which repre-
sent the measurement of the traveled distance or angle.
Incremental encoders operate on the principle of optoelectronic
scanning of dividing discs with the transmitted light principle. The
light source is a light emitting diode (LED). The light-dark modula-
tion generated as the encoder shaft rotates is picked up by pho-
toelectronic elements. With an appropriate arrangement of the line
pattern on the dividing disk connected to the shaft and the fixed
aperture, the photoelectronic elements provide two trace signals
A and B at 90° to one another, as well as a reference signal R.
The encoder electronics amplify these signals and convert them
to different output levels.
Signal levels
The following signal levels are available for the incremental
encoders:
■
Technical specifications
1)
With recommended cable and input circuitry of the downstream electronics,
observe max. permissible cable length of module to be evaluated.
Signal level
Benefits
Analog signals sin/cos
with level 1 V
pp
The analog signal allows the digitization of the
trace signals. In order to obtain a fine resolution,
the signals are interpolated in the higher-level
controller.
RS422 differential signals
(TTL)
The resolution can be quadrupled by means of
edge evaluation.
HTL (High Voltage
Transistor Logic)
Built-on encoders with an HTL interface are
designed for applications with digital inputs with
a 24 V level. The resolution can be quadrupled
by means of edge evaluation.
Article No.
6FX2001-3
....
6FX2001-2
....
6FX2001-4...0
Product name
Motion control encoder
Motion control encoder
Motion control encoder
Product designation
Incremental encoder
with sin/cos 1 V
pp
Incremental encoder
with RS422 (TTL)
Incremental encoder
with HTL
Operating voltage DC
V
p
on encoder
V
5 ± 10 %
5 ± 10 %
or
10 ... 30
10 ... 30
Limit frequency, typical
kHz
≥
180 (- 3 dB)
≥
450 (- 6 dB)
–
–
Scanning frequency, maximum
kHz
–
300
300
No-load current consumption,
maximum
mA
150
150
150
Resolution, maximum
S/R
2500
5000
2500
Signal level
Sinusoidal 1 V
pp
RS422 (TTL)
V
H
≥
21 V
with
I
H
= 20 mA at 24 V
V
L
≤
2.8 V
with
I
L
= 20 mA at 24 V
Outputs protected against
short-circuit to 0 V
Yes
Briefly
Yes
Yes
Briefly
Switching time (10 … 90 %)
rise/fall time
t
+
/t
-
(for 1 m (3.28 ft) cable and
recommended input circuit)
ns
–
≤
50
≤
200
Phase angle, signal A to B
Edge spacing
Degrees
90 ± 10
90
90
• At 300 kHz
μs
–
≥
0.45
≥
0.45
Cable length to downstream
electronics, maximum
1)
m (ft)
150 (492)
100 (328) without fault signal
50 (164) with fault signal
300 (984)
Accuracy
arcsec
± 18 mech. × 3600/PPR count
z
± 18 mech. × 3600/PPR count
z
± 18 mech. × 3600/PPR count
z
LED failure monitoring
–
High-resistance driver
High-resistance driver
Maximum mechanical speed
rpm
12000
12000
12000
Starting torque at 20 °C (68 °F)
Nm
(lb
f
-ft)
≤
0.01 (0.01)
≤
0.01 (0.01)
≤
0.01 (0.01)
S/R = signals/revolution
© Siemens AG 2017