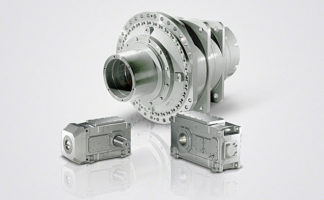
9/86
Siemens D 21.4 · 2017
SIMOTICS main motors
SIMOTICS M asynchronous and synchronous motors for SINAMICS S120
Selection guides for SIMOTICS M-1PH8 motors
> Mounted holding brakes
9
■
Overview
Mounted holding brake for 1PH8 motors
A brake can be mounted on the DE of 1PH808 to 1PH822
motors.
These brakes are electromagnetic units for dry-running opera-
tion. An electromagnetic field is used to release the brake which
is applied using spring force. They operate in accordance with
the quiescent current principle, i.e. when no current is flowing,
the spring-operated brake brakes and holds the drive. When
power is applied to the brake, it is released and the drive is free
to rotate.
In the event of a power failure or an emergency stop, the drive is
braked from its current speed down to standstill.
Connection of the brakes (must be provided by the customer)
•
Alternating voltage 230 V 1 AC, 50/60 Hz
•
Direct voltage 24 V DC up to 1PH816
The brake module is designed for an ambient temperature of
-5 °C to +40 °C (23 °F to 104 °F).
The maximum speed of a motor with brake is limited to the
maximum speed of the brake (refer to the table).
The holding brakes for 1PH818 and 1PH822 are not UL-ap-
proved. As a consequence, these motors do not have the cUR
marking when mounted on brakes.
Explanation of terms
Note: You will find additional information on mounted holding
brakes in the Configuration Manual.
Motor
Type
Brake type
Holding
torque
Maxi-
mum
speed
Moment
of inertia
Weight
Coil current
Single
switch-
ing
energy,
perm.
Moment
of inertia,
total
(emer-
gency
stop)
Speed
(emer-
gency
stop)
Number
of emer-
gency
stops
1)
Open-
ing
time
Clos-
ing
time
n
max
J
Br
m
Br
230 V AC
±10 %
24 V DC
±10 %
W
E
J
tot
n
z
Nm
(lb
f
-ft)
rpm
kgm
2
(lb
f
-in-s
2
)
kg
(lb)
A
A
kJ
kgm
2
(lb
f
-in-s
2
)
rpm
ms
ms
1PH808
Size 13
29
(21.4)
5000
0.00093
(0.01)
10
(22.0)
0.8
4.1
2.2
0.0174
(0.15)
4800
2000
150
40
1PH810
Size 19
60 ... 150
(44.3 ...111)
5000
0.0048
(0.04)
21
(46.3)
1.0
4.7
7
0.063
(0.56)
4500
2000
500
60
1PH813
Size 24
140 ... 310
(103...229)
4500
0.0141
(0.12)
46
(101)
1.3
6.3
15.5
0.218
(1.93)
3600
2000
650
100
1PH816
Size 29
280 ... 500
(207 ... 369)
4000
0.0266
(0.24)
66
(146)
1.4
6.7
24
0.456
(4.04)
3100
2000
750
150
1PH818
NFF-A 63
1000
(738)
3500
0.022
(0.19)
63
(139)
2.2
–
98
1.3
(11.5)
3000
2000
300
80
1PH822
NFF-A 100
1600
(1180)
3100
0.051
(0.45)
88
(194)
2.7
–
210
3.9
(34.52
2800
1200
300
100
Holding torque
For 1PH810 to 1PH816 motors, the holding torque
can be continuously set in the specified value range
using a setting ring. The dynamic braking torque is
approximately 70 % of the set holding torque.
Single switching
energy,
perm.
W
E
Perm. switching energy for emergency stop,
W
E
=
J
tot.
×
n
2
/182.4
×
10
-3
(
J
in kgm
2
,
n
in rpm)
Service life switching
energy
W
max
Max. possible switching energy of the brake
(for emergency stop) until the brake linings must be
replaced,
W
max
=
W
E
× z.
Number of
emergency stops z
The specified number of emergency stops refers to
the specified conditions.
A conversion can be made for operation under
different conditions: Number of emergency stops
z =
W
max
/
W
E
Coil current
Current to release the brake.
Opening time
Separating time until the brake releases
(the specified values refer to the maximum braking
torque and rated voltage).
Closing time
Interlocking time until the brake closes
(values refer to the maximum braking torque and
with rated voltage).
© Siemens AG 2017