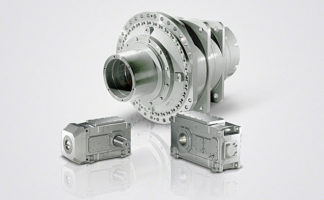
7/11
Siemens D 21.4 · 2017
SINAMICS S120 drive system
Control Units
CU310-2 Control Units for single-axis drives
7
■
Overview
CU310-2 PN and CU310-2 DP Control Units
The CU310-2 Control Unit that is designed for the communication
and open-loop/closed-loop control functions of a SINAMICS S120
(AC/AC) is combined with the PM240-2 Power Module (can be
used from firmware V4.8) to create a high-performance single-
axis drive. A PROFINET (PN) variant and a PROFIBUS (DP)
variant are available for fieldbus communication.
CompactFlash card for CU310-2 Control Units
The CompactFlash card contains the firmware and parameter
settings. The CompactFlash card is plugged into the appropri-
ate slot on the CU310-2 Control Unit.
A CU310-2 Control Unit can perform the communication, open-
loop and closed-loop control functions for one Power Module.
The performance expansion is not required in this case.
In addition to the firmware, the CompactFlash Card also contains
licensing codes which are required to enable firmware options.
In addition to the Article No., the following firmware options can
currently be ordered:
•
Safety Integrated Extended Functions, order code
F01
•
High output frequency
1)
, order code
J01
•
DCB Extension, order code
U01
After the appropriate license has been purchased via the WEB
License Manager available on the Internet, firmware options can
also be subsequently enabled.
Further information is available on the Internet at
/automation/license
■
Design
The CU310-2 Control Unit has the following connections and
interfaces as standard:
•
Fieldbus interface
- CU310-2 PN: 1 PROFINET interface with 2 ports
(RJ45 sockets) with PROFIdrive V4 profile
- CU310-2 DP: 1 PROFIBUS interface with PROFIdrive V4
profile
•
1
DRIVE-CLiQ socket for communication with the DRIVE-CLiQ
motor or other DRIVE-CLiQ devices (e.g. Sensor Modules or
Terminal Modules)
•
1 encoder evaluation for evaluating the following encoder
signals
- Incremental encoder TTL/HTL
- SSI encoder without incremental signals
•
1 PE/protective conductor connection
•
1 connection for the electronics power supply via the 24 V DC
supply connector
•
1 temperature sensor input for KTY84-130, Pt1000 or PTC
(Pt1000 can be used from firmware V4.7 HF17)
•
3 parameterizable, fail-safe (can be used with firmware V4.5
and higher) digital inputs (floating) or alternatively
6 parameterizable digital inputs (floating).
The fail-safe digital inputs can be routed, i.e. they can be
routed via PROFIsafe to a higher-level controller.
•
5 parameterizable digital inputs (floating)
•
1 parameterizable, fail-safe (can be used with firmware V4.5
and higher) digital input (floating) or alternatively 1 digital
output (floating)
2)
•
8 parameterizable bidirectional digital inputs/outputs
(non-floating)
2)
•
1 analog input, either ± 10 V (resolution 12 bits + sign) or
± 20 mA (11 bits + sign)
•
1 Ethernet interface (RJ45 socket) for commissioning and
diagnostics
•
1 slot for the CompactFlash card on which firmware and
parameters are stored
•
1 PM-IF interface for communication with the Power Modules
in blocksize format
•
3 test sockets and one reference ground for commissioning
support
•
1 interface to the BOP20 Basic Operator Panel
The status of the CU310-2 Control Unit is indicated using
multi-color LEDs.
A BOP20 Basic Operator Panel can also be snapped directly
onto the CU310-2 Control Unit for diagnostics.
As the firmware and parameter settings are stored on a plug-in
CompactFlash card, the Control Unit can be changed without
the need for software tools.
1)
For further information, see
2)
A 24 V supply voltage must be connected to terminal X124 for the digital
outputs to be used.
© Siemens AG 2017