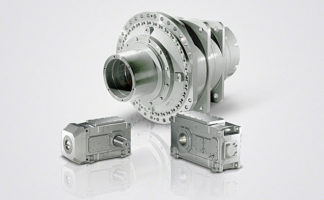
7/10
Siemens D 21.4 · 2017
SINAMICS S120 drive system
Control Units
7
■
Overview
(continued)
BICO technology
Every drive object contains a large number of input and output
variables which can be freely and independently interconnected
using Binector Connector Technology (BICO). A binector is a
logic signal which can assume the value 0 or 1. A connector is a
numerical value, e.g. the actual speed or current setpoint.
Basic positioner (EPos)
The EPos basic positioner provides powerful and precise posi-
tioning functions. Due to its flexibility and adaptability, the EPos
basic positioner can be used for a wide range of positioning
tasks. The functions are easy to use during both commissioning
and operation, and the comprehensive monitoring functions are
very powerful. Many applications can be implemented without
external position control systems.
Additional information about the basic positioner (EPos) is
provided in section Technology functions.
Technology controller (PID)
The technology controller is designed as a PID controller. It is
suitable for implementing controls for regulating variables such
as fill level, temperature, tension, pressure, flow rate and dancer
position.
Additional information about the technology controller (PID) is
provided in section Firmware functionality.
SINAMICS Drive Control Chart (SINAMICS DCC)
SINAMICS DCC expands the scope of device functions by
means of freely available closed-loop control, arithmetic and
logic blocks and offers a means by which proprietary technolog-
ical functions can be graphically configured in the SINAMICS
drive system. In addition, local data processing in the drive
supports the implementation of modular machine concepts and
results in an increase in the overall machine performance.
Additional information about the Drive Control Chart (DCC) is
provided in section Engineering tools.
SINAMICS Technology Extensions (SINAMICS TEC)
The SINAMICS TEC are configurable functions or Siemens tech-
nologies that can be added to extend firmware functions. These
extensions are designed to allow implementation of highly com-
plex, application-specific tasks for various sectors - such as
storage and retrieval machines.
Additional information about Technology Extensions (TEC) is
provided in section Technology functions.
Integral safety functions (Safety Integrated)
The Control Units support comprehensive safety functions.
The integrated safety functions are the
Safety Integrated Basic Functions
•
STO = Safe Torque Off
•
SBC = Safe Brake Control
•
SS1 = Safe Stop 1
And the
Safety Integrated Extended Functions
that require a license
•
SS1 with SBR/SAM = Safe Stop 1 with Safe Brake Ramp/
Safe Acceleration Monitor
•
SS2 = Safe Stop 2
•
SOS = Safe Operating Stop
•
SBT = Safe Brake Test
•
SLS = Safely Limited Speed
•
SSM = Safe Speed Monitor
•
SDI = Safe Direction
•
SLP = Safely-Limited Position
•
SP = Safe Position
(abbreviations in accordance with IEC 61800-5-2)
If the integrated safety functions are used, licenses, supplemen-
tary system components such as TM54F terminal modules, or
suitable safety controls will be necessary.
Additional information about the integrated safety functions is
provided in section Safety Integrated.
Diagnostics optimally supported by trace function
The time characteristics of input and output variables associated
with drive objects can be measured by the integrated trace
function and displayed using the STARTER commissioning tool.
The trace can record up to 4 signals simultaneously. A recording
can be triggered dependent on freely selectable boundary
conditions, e.g. the value of an input or output variable.
© Siemens AG 2017