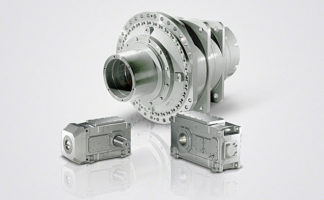
6/3
Siemens D 21.4 · 2017
Technology functions
Basic positioner EPos
6
■
Overview
(continued)
Functionality of the EPos basic positioner
Lower-level closed-loop position control with the following
essential components
•
Position actual value sensing (including the lower-level
measuring probe evaluation and reference mark search)
•
Position controller (including limits, adaptation and pre-control
calculation)
•
Monitoring functions (standstill, positioning and dynamic
following error monitoring, cam signals)
Mechanical system
•
Backlash compensation
•
Modulo offset
Limitations
•
Speed/acceleration/delay/jerk limitation
•
Software limit switches (traversing range limitation by means
of position setpoint evaluation)
•
Stop cams (traversing range limitation using hardware limit
switch evaluation)
Referencing or adjustment
•
Set reference point (for an axis at standstill)
•
Search for reference (separate mode including reversing cam
functionality, automatic reversal of direction, homing to "output
cam and encoder zero mark" or only "encoder zero mark" or
"external zero mark (BERO)")
•
Flying referencing (seamless referencing possible during
"normal" traversing with the aid of the measuring input evalu-
ation; generally evaluation, e.g. of a BERO. Subordinate
function for the modes "jog", "direct setpoint input/MDI" and
"traversing blocks")
•
Absolute encoder alignment
Traversing blocks mode (64 traversing blocks)
•
Positioning using traversing blocks that can be stored in the
drive unit including block change enable conditions and
specific tasks for an axis that was previously referenced
•
Configuring traversing blocks using the traversing block
editor in the commissioning tool of the SINAMICS drive family
•
A traversing block contains the following information:
- Job number and job (e.g. positioning, waiting, GOTO block
jump, setting of binary outputs, travel to fixed endstop)
- Motion parameters (target position, velocity, override for
acceleration and deceleration)
- Mode (e.g.: hide block, continuation conditions such as
"Continue_with_stop", "Continue_flying" and
"Continue_externally using high-speed probe inputs")
- Job parameters (e.g. wait time, block step conditions)
Direct setpoint input (MDI) mode
•
Positioning (absolute, relative) and setting-up (endless
closed-loop position control) using direct setpoint inputs
(e.g. via the PLC using process data)
•
It is always possible to influence the motion parameters during
traversing (on-the-fly setpoint acceptance) as well as for on-
the-fly changes between the setup and positioning modes.
•
The direct setpoint specification operating mode (MDI) can
also be used in the relative positioning or setup mode if the
axis is not referenced. This means that on-the-fly synchroni-
zation and re-referencing can be carried out using "flying
referencing".
Jog mode
•
Closed-loop position controlled traversing of the axis with
"endless position controlled" or "jog incremental" modes
(traverse through a "step width"), which can be toggled
between
© Siemens AG 2017