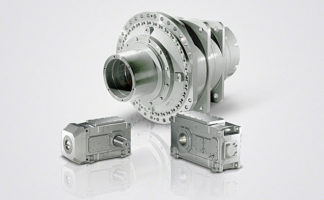
5/8
Siemens D 21.4 · 2017
Communication
PROFIBUS
5
■
Overview
PROFIBUS – the proven, rugged bus system for automation
engineering applications
The requirements of users for an open, non-proprietary
communication system have resulted in the specification and
standardization of the PROFIBUS protocol.
PROFIBUS defines the technical and functional features of a
serial fieldbus system, with which the distributed field auto-
mation devices in the lower area (sensor/actuator level) can be
networked up to the mid performance range (cell level).
Standardization according to IEC 61158/EN 50170 secures your
investments for the future.
Using the conformity and interoperability test performed by the
test laboratories authorized by PROFIBUS & PROFINET Inter-
national (PI) and the certification of the devices by PI, users have
the security of knowing that the quality and functionality is
guaranteed, even in multi-vendor installations.
PROFIBUS versions
Two different PROFIBUS versions have been defined in order to
comply with the widely varying requirements at field level:
•
PROFIBUS PA (P
rocess A
utomation) – the version for appli-
cations in process automation. PROFIBUS PA uses the
intrinsically safe transmission technology specified in
IEC 61158-2.
•
PROFIBUS DP (D
istributed P
eriphery) – this version, which is
optimized for speed, is specifically tailored to the communi-
cation of automation systems with distributed I/O stations and
drives. PROFIBUS DP sets itself apart as a result of very short
response times and high noise immunity, and replaces cost-
intensive, parallel signal transfer with 24 V and measured
value transfer utilizing 0/4 … 20 mA technology.
■
Design
Bus participants on PROFIBUS DP
PROFIBUS DP makes a distinction between two different master
classes and one slave class:
DP master class 1
For PROFIBUS DP, DP master class 1 is the central component.
In a defined and continually repeating message cycle the
central master station exchanges information with distributed
stations (DP slaves).
DP master class 2
Devices of this type (programming, configuring or operator
control devices) are used during commissioning, for configuring
the DP system, for diagnostics or for operating the active plant
or system. A DP master class 2 can, for example, read input,
output, diagnostic and configuration data of the slaves.
DP slave
A DP slave is an I/O device which receives output information or
setpoints from the DP master, and as response, returns input in-
formation, measured values and actual values to the DP master.
A DP slave never sends data automatically, but only when re-
quested by the DP master.
The quantity of input and output information depends on the
device, and for each DP slave in each send direction can be a
maximum of 244 bytes.
■
Function
Functional scope in DP masters and DP slaves
The functional scope can differ between DP masters and DP
slaves. The functional scope is different for DP-V0, DP-V1 and
DP-V2.
DP-V0 communication functions
The DP-V0 master functions comprise the functions "Configura-
tion", "Parameter Assignment", "Read Diagnostics Data" as well
as cyclic reading of input data/actual values and writing output
data/setpoints.
DP-V1 communication functions
The DP-V1 function expansions make it possible to perform
acyclic read and write functions as well as processing cyclic
data communication. This type of slave must be supplied with
extensive parameterization data during start-up and during nor-
mal operation. These acyclically transferred parameterization
data are only rarely changed in comparison to the cyclic set-
points, actual values, and measured values, and are transferred
at lower priority in parallel with the cyclic high-speed user data
transfer. Detailed diagnostic information can be transferred in
the same way.
DP-V2 communication functions
The extended DP-V2 master functions mainly comprise functions
for isochronous operation and direct data exchange between
DP slaves.
•
Isochronous mode:
Isochronous mode is implemented by means of an equidistant
clock signal in the bus system. This cyclic, equidistant cycle
is sent by the DP master to all bus nodes in the form of a
Global Control Telegram. Master and slaves can then synchro-
nize their applications with this signal. The signal jitter be-
tween cycles is less than 1
μ
s.
•
Slave-to-slave communication:
The "publisher/subscriber" model is used to implement
slave-to-slave communication. Slaves declared as publishers
make their input data/actual values and measured values
available to other slaves, the subscribers, for reading. This is
performed by sending the response frame to the master as a
broadcast. Slave-to-slave communication is therefore a cyclic
process.
■
Integration
PROFIBUS with SINAMICS
SINAMICS uses the PROFIBUS DP protocol. SINAMICS drives
can only be used as DP slaves.
G_PM10_XX_00144
© Siemens AG 2017