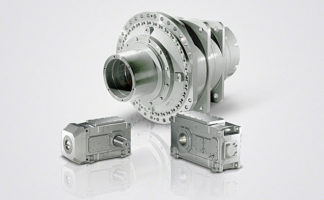
4/3
Siemens D 21.4 · 2017
Energy efficiency
Energy-efficient drives
4
■
Overview
Energy-efficient SINAMICS drives save energy in an
intelligent way
Exploit energy-saving potential and optimize energy consump-
tion: You can – with intelligent SINAMICS drives Depending on
the application in question, energy consumption can be con-
trolled by motor speed adjustment to suit the individual process
and achieve the greatest possible energy savings. The energy
consumption of drives for turbomachines can be cut by as much
as 60 %. Regenerative feedback is also an option for many ap-
plications. Our portfolio of frequency inverters is the most com-
prehensive on the market and the first choice for anyone seeking
an energy-efficient drive – at low-voltage or medium-voltage
level.
Energy-efficient drives with intelligent functions
Depending on the application and load profile, the intelligent
energy-saving functions of SINAMICS drives can cut energy
consumption.
PROFIenergy
Provides energy-related status data for the system
components to create transparency for the energy
management; energy savings by selective shut-
down of plants or plant sections.
ECO mode
In ECO mode, the operating point of the motor in
the partial-load range is automatically adjusted
and optimized. This reduces motor losses, for
example, in machines that do not need a high
torque over the entire operating range.
Hibernation mode
Variable-speed drives that are not required to
operate continuously are switched to standby or
“Hibernation mode". The drive is restarted again
as soon as it is needed.
Bypass mode
In bypass mode it is possible to "bypass" the in-
verter electrically as soon as the motor is frequently
operating close to its rated speed. This solution
helps to reduce inverter losses and so increase
overall efficiency.
Cascading
In pump, fan and compressor applications
involving high outputs, the entire power demand
is distributed among several motors. Phased con-
nection and disconnection by means of partially or
fully controlled cascades in combination with in-
verters make a drive system more energy-efficient.
Energy balancing
Through the use of inverters with coupled drives,
energy is exchanged through the common DC link.
Through the direct energy exchange from one in-
verter to the next, it is possible to minimize power
losses in the system.
Reactive power compensation
The use of SINAMICS inverters with Active Line
Modules reduces the capacitive and/or inductive
reactive power in the machine. It is then possible to
dispense with costly reactive power compensation
systems.
Kinetic energy buffering
With dynamic reversing operations in single-axis
and multi-axis systems, the kinetic energy avail-
able in the system is reused. A motor connected to
the common DC link is used to buffer kinetic
energy.
Electrical energy buffering
With dynamic reversing operations in single-axis
and multi-axis systems, the kinetic energy avail-
able in the system is reused. A capacitor module
connected to the common DC link is used to buffer
electrical energy.
Optimized pulse pattern
Thanks to optimized clock frequency and pulse
pattern, SINAMICS G and SINAMICS S are per-
fectly suited to SIMOTICS motors. The benefits:
Optimization of performance and system effi-
ciency, reduced system losses as well as lower
temperature and noise levels.
Energy usage counter/Energy saving counter
Actual energy usage can be displayed during
operation. Furthermore, an energy saving counter
can be installed to indicate the cumulative energy
savings during machine operation as compared to
a fixed-speed application.
Regenerative feedback
In conventional drive systems, the energy pro-
duced during braking is converted to heat using
braking resistors. SINAMICS G and SINAMICS S
inverters with regenerative feedback capability
need no braking resistor, and supply the resulting
braking energy back into the line.
© Siemens AG 2017