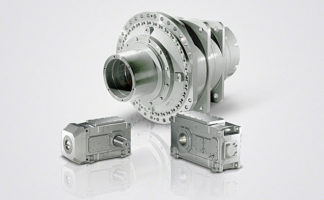
8/7
Siemens D 21.4 · 2017
SIMOTICS servomotors
Technical definitions for AC motors
8
■
Overview
(continued)
Balancing according to DIN ISO 8821
In addition to the balance quality of the motor, the vibration quality
of motors with mounted belt pulleys and coupling is essentially
determined by the balance quality of the mounted component.
If the motor and mounted component are separately balanced
before they are assembled, then the process used to balance
the belt pulley or coupling must be adapted to the motor balanc-
ing type. The following different balancing methods are used on
motors of types SIMOTICS M-1PH8:
•
Half-key balancing
•
Full-key balancing
•
Plain shaft extension
The letter H (half key) or F (full key) is printed on the shaft exten-
sion face to identify a half-key balanced or a full-key balanced
SIMOTICS M-1PH8 motor.
SIMOTICS S-1FT7/S-1FK7 motors with feather key are always
half-key balanced.
In general, motors with a plain shaft are recommended for sys-
tems with the most stringent vibrational quality requirements.
For
full-key balanced motors, we recommend belt pulleys with two
opposite keyways, but only one feather key in the shaft extension.
Vibration stress, immitted vibration values
The following maximum permissible vibration stress limits at full
reliability performance apply only to SIMOTICS S-1FT7/1FK7
permanent-magnet servomotors.
Vibration stress according to DIN ISO 10816:
For motors with forced ventilation, the limit values for axial and
radial acceleration are limited to 10 m/s
2
(32.8 ft/s
2
)
For all main motors of type SIMOTICS M-1PH8, the following lim-
its are valid for (immitted) vibration values introduced into the
motor from outside:
For all torque motors of type SIMOTICS T-1FW3, the following
limits are valid for (immitted) vibration values introduced into the
motor from outside:
Coolant temperature (ambient temperature) and installation
altitude for motors with natural cooling and forced
ventilation
Operation (unrestricted): -15
°C to +40
°C (+5 to 104 °F)
The rated power (rated torque) is applicable to continuous
duty (S1) in accordance with EN 60034-1 at rated frequency, a
coolant temperature of 40 °C (104 °F) and an installation altitude
of up to 1000 m (3281 ft) above sea level.
Apart from the SIMOTICS M-1PH8 motors, all motors are de-
signed for temperature class 155 (F) and utilized in accordance
with temperature class 155 (F). The SIMOTICS M-1PH8 motors
are designed for temperature class 180 (H). For all other condi-
tions, the factors given in the table below must be applied to
determine the permissible output (torque).
The coolant temperature and installation altitude are rounded to
5 °C (41 °F) and 500 m (1640 ft) respectively.
Vibration
frequency
Vibration values for
1FT7/1FK7
(naturally cooled and water-cooled)
10 ... 2000 Hz
Vibration velocity
V
rms
≤
4.5 mm/s (0.18 in/s)
Vibration acceleration
a
axial
≤
25 m/s
2
(82.0 ft/s
2
)
Vibration acceleration
a
radial
≤
50 m/s
2
(164.0 ft/s
2
)
Vibration
frequency
Vibration values for
1PH808/1PH810/1PH813/1PH816
< 6.3 Hz
Vibration displacement s
≤
0.16 mm (0.006 in)
6.3 ... 250 Hz
Vibration velocity
V
rms
≤
4.5 mm/s (0.18 in/s)
> 250 Hz
Vibration acceleration
a
≤
10 m/s
2
(32.8 ft/s
2
)
Vibration
frequency
Vibration values for
1PH818/1PH822/1PH828
< 6.3 Hz
Vibration displacement
s
≤
0.26 mm (0.010 in)
6.3 ... 63 Hz
Vibration velocity
V
rms
≤
7.1 mm/s (0.28 in/s)
> 63 Hz
Vibration acceleration
a
≤
4.0 m/s
2
(13.12 ft/s
2
)
Vibration
frequency
Vibration values for
1FW3
< 6.3 Hz
Vibration displacement
s
≤
0.26 mm (0.010 in)
6.3 ... 63 Hz
Vibration velocity
V
rms
≤
7.1 mm/s (0.28 in/s)
> 63 Hz
Vibration acceleration
a
≤
4.0 m/s
2
(13.12 ft/s
2
)
Installation
altitude above
sea level
Coolant temperature
(ambient temperature)
m (ft)
< 30 °C
(86 °F)
30 ... 40 °C
(86 ... 104 °F)
45 °C
(113 °F)
50 °C
(122 °F)
1000 (3281)
1.07
1.00
0.96
0.92
1500 (4922)
1.04
0.97
0.93
0.89
2000 (6562)
1.00
0.94
0.90
0.86
2500 (8203)
0.96
0.90
0.86
0.83
3000 (9843)
0.92
0.86
0.82
0.79
3500 (11484)
0.88
0.82
0.79
0.75
4000 (13124)
0.82
0.77
0.74
0.71
© Siemens AG 2017