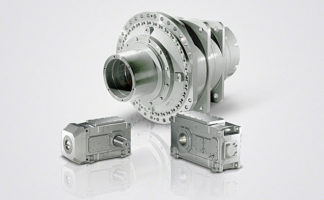
3/9
Siemens D 21.4 · 2017
Safety Integrated
Safety Integrated
3
■
Function
Safe Position (SP)
The SP function transfers the actual position values determined
safely in the drive over safe PROFIsafe communication to a
safety control.
Effect
In contrast to the SLP function that monitors the current actual
position value against a limit and, in the case of an overshoot,
activates a drive-integrated fault reaction, SP transfers the
current actual position values to the safety control. Position
monitoring is implemented in the safety program of the control.
Extended PROFIsafe telegrams are available for transferring the
position values. The position values can be transferred in 16-bit
or 32-bit resolution, as required. A time stamp is also transferred
with the position values.
Application
Tailor-made safety concepts can be created using the SP func-
tion. It is ideal for use on machines that require flexible safety
functions. It is extremely versatile and can be used, for example,
to implement safe, axis-specific range detection by means of
safe cams. The SP function can also be used to implement multi-
axis safety concepts, multi-dimensional protection areas and
zone concepts.
Customer benefits
Position monitoring or speed monitoring is implemented in the
safety program of the control, so the user has the flexibility for
implementing tailor-made safety functions. The reaction to a limit
overshoot must also be specified in the safety program. This
means a higher initial programming outlay, but it does offer the
opportunity for initiating different fault reactions.
Basic Functions and Extended Functions
The Safety Integrated functions are grouped into Basic Functions
and Extended Functions.
The Basic Functions are included in the standard scope of supply.
The Extended Functions must be activated by a license.
•
Basic Functions
- Safe Torque Off (STO)
- Safe Brake Control (SBC)
- Safe Stop 1 (SS1)
•
Extended Functions
- Safe Stop 1 (SS1) with SBR or SAM
- Safe Stop 2 (SS2) with SBR or SAM
- Safe Operating Stop (SOS)
- Safely-Limited Speed (SLS)
- Safe Speed Monitor (SSM)
- Safe Direction (SDI)
- Safely-Limited Position (SLP)
- Safe Position (SP)
- Safe Brake Test (SBT) diagnostic function
For the Extended Functions SS1 and SS2 with SAM, safe
acceleration monitoring (SAM) is performed during braking
to identify any faults already during the braking phase.
With SS1 and SS2, a Safe Brake Ramp (SBR) can be configured
as an alternative.
The Basic Functions – activated via on-board terminals on the
device, TM54F Terminal Module or via PROFIsafe – do not
require an encoder.
Activation of the integrated safety functions
The safety functions for SINAMICS drives can be activated via
terminals, e.g. for use of a conventional safety circuit.
For standalone safety solutions for small to medium sized
applications, it is frequently sufficient that the various sensing
components are directly hardwired to the drive.
For integrated safety solutions, the safety-relevant sequences
are generally processed and coordinated in the fail-safe
SIMATIC controller. Here, the system components communicate
via the PROFINET or PROFIBUS fieldbus. The safety functions
are controlled via the safe PROFIsafe communication protocol.
SINAMICS drives can be easily integrated into the plant or
system topology.
PROFIsafe
SINAMICS drives support the PROFIsafe profile based on
PROFINET as well as on PROFIBUS.
PROFIsafe is an open communications standard that supports
standard and safety-related communication over the same
communication path (wired or wireless). A second, separate bus
system is therefore not necessary. The telegrams that are sent
are continually monitored to ensure safety-relevant communi-
cation.
Possible errors such as telegrams that have been lost, repeated
or received in the incorrect sequence are avoided. This is done
by consecutively numbering the telegrams in a safety-relevant
fashion, monitoring their reception within a defined time and
transferring an ID for transmitter and receiver of a telegram.
A CRC (cyclic redundancy check) data security mechanism
is also used.
SP
G_D211_XX_00309a
© Siemens AG 2017