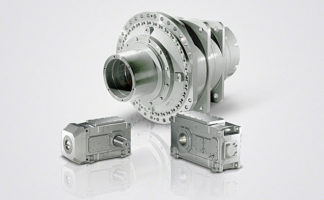
7/301
Siemens D 21.4 · 2017
SINAMICS S120 drive system
Supplementary system components
Encoder system connection
> SMC20 Sensor Module Cabinet-Mounted
7
■
Overview
SMC20 Sensor Module Cabinet-Mounted
The SMC20 Sensor Module Cabinet-Mounted is required to
evaluate the encoder signals of motors without a DRIVE-CLiQ
interface. External encoders can also be connected via the
SMC20.
The following encoder signals can be evaluated:
•
Incremental encoder sin/cos 1 V
pp
•
Absolute encoder EnDat 2.1
•
SSI encoder with incremental signals sin/cos 1 V
pp
(firmware version 2.4 and later)
The motor temperature can also be sensed using a PTC
thermistor KTY84-130, Pt1000 or PTC.
■
Design
The SMC20 Sensor Module Cabinet-Mounted features the
following connections and interfaces as standard:
•
1 encoder connection including motor temperature sensing
(KTY84-130, Pt1000 or PTC) via SUB-D connector
•
1 DRIVE-CLiQ interface
•
1 connection for the electronics power supply via the 24 V DC
supply connector
•
1 PE (protective earth) connection
The status of the SMC20 Sensor Module Cabinet-Mounted is
indicated via a multi-color LED.
The SMC20 Sensor Module Cabinet-Mounted can be snapped
onto a TH 35 standard mounting rail in accordance with
EN 60715 (IEC 60715).
The signal cable shield is connected via the encoder system
connector and can also be connected to the SMC20 Sensor
Module Cabinet-Mounted via a shield connection terminal, e.g.
Phoenix Contact type SK8 or Weidmüller type KLBÜ CO 1. The
shield connection terminal must not be used as a strain relief
mechanism.
■
Integration
SMC20 Sensor Modules Cabinet-Mounted communicate with a
Control Unit via DRIVE-CLiQ.
■
Selection and ordering data
■
Technical specifications
Description
Article No.
SMC20 Sensor Module Cabinet-Mounted
Without DRIVE-CLiQ cable
6SL3055-0AA00-5BA3
Accessories for re-ordering
Dust protection blanking plugs
(50 units)
For DRIVE-CLiQ port
6SL3066-4CA00-0AA0
SMC20 Sensor Module
Cabinet-Mounted
6SL3055-0AA00-5BA3
Current requirement, max.
at 24 V DC,
without taking encoder into account
0.2 A
• Conductor cross-section, max.
2.5 mm
2
• Fuse protection, max.
20 A
Power loss, max.
10 W
Encoders which can be evaluated
• Incremental encoder
sin/cos 1 V
pp
• Absolute encoder EnDat 2.1
• SSI encoder with
incremental signals
sin/cos 1 V
pp
(firmware
version 2.4 and later)
• Encoder supply
5 V DC/0.35 A
• Encoder frequency incremental signals,
max.
500 kHz
• Signal subdivision (interpolation), max.
16384 times (14 bits)
• SSI baud rate
100 ... 1000 kBaud
• Cable length to encoder, max.
100 m (328 ft)
PE connection
M4 screw
Dimensions
• Width
30 mm (1.18 in)
• Height
150 mm (5.91 in)
• Depth
111 mm (4.37 in)
Weight, approx.
0.45 kg (0.99 lb)
Certificate of suitability
cULus
© Siemens AG 2017