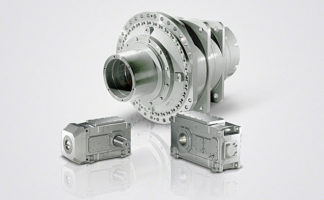
3/4
Siemens D 21.4 · 2017
Safety Integrated
Safety Integrated
3
■
Function
Safe Torque Off (STO)
The STO function is the most common and basic drive-integrated
safety function. It ensures that no torque-generating energy can
continue to affect a motor and prevents unintentional start-ups.
Effect
This function is a mechanism that prevents the drive from restart-
ing unexpectedly, in accordance with EN 60204-1, Section 5.4.
The STO function suppresses the drive pulses (corresponds to
Stop Category 0 according to EN 60204-1). The drive is reliably
torque-free. This state is monitored internally in the drive.
Application
STO has the immediate effect that the drive cannot supply any
torque-generating energy. STO can be used wherever the drive
will naturally reach a standstill due to load torque or friction in a
sufficiently short time or when "coasting down" of the drive will
not have any relevance for safety.
STO makes it possible for persons to work safely when the
protective door is open (restart interlock) and is used on ma-
chines/installations with moving axes, e.g. on handling or
conveyor systems.
Customer benefits
The advantage of the integrated STO safety function compared
to standard safety technology using electromechanical switch-
gear is the elimination of separate components and the effort
that would be required to wire and service them. Because of the
fast electronic switching times, the function provides a shorter
reaction time than the conventional solution comprising electro-
mechanical components.
Safe Stop 1 (SS1)
The SS1 function causes a motor to stop rapidly and safely and
switches the motor to torque-free mode after coming to a stand-
still by activating STO.
Effect
The SS1 function can safely stop the drive in accordance with
EN 60204-1, Stop Category 1. When the SS1 function is selected,
the drive brakes autonomously along a quick-stop ramp and
automatically activates the Safe Torque Off and Safe Brake
Control functions (if configured) when the parameterized safety
delay time expires.
If the variant "SS1 with external stop (SS1E)" is parameterized,
the drive does not brake autonomously when the function is
selected. In this case, the higher-level control must bring the
drive to a standstill within a parameterized STO transition time.
The SBR (Safe Brake Ramp) and SAM (Safe Acceleration
Monitor) functions are not active. SS1E is a useful function for
drives that need to be stopped as a group by the Motion Control
system in order to prevent potential damage to the machine or
product.
Application
The SS1 function is used when, in the event of a safety-relevant
incident, the drive must stop as quickly as possible with a sub-
sequent transition into the STO state (e.g. EMERGENCY STOP).
It is thus used to bring large centrifugal masses to a stop as
quickly as possible for the safety of the operating personnel,
or to brake motors at high speeds as quickly as possible.
Examples of typical applications are saws, grinding machine
spindles, centrifuges, winders and storage and retrieval ma-
chines.
Customer benefits
The targeted stopping of a drive by means of SS1 reduces the
risk of danger, increases the productivity of a machine, and
allows the safety clearances in a machine to be reduced. The
principle is to bring the drive actively to a standstill, compared
with just using the STO function. Complex mechanical brakes
that are susceptible to wear are not normally required to brake
the motor.
STO
v
t
G_D211_XX_00304
STO
v
t
G_D211_XX_00305
© Siemens AG 2017