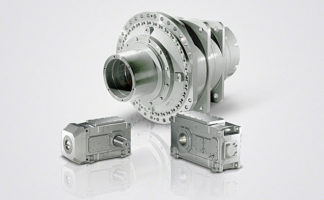
7/113
Siemens D 21.4 · 2017
SINAMICS S120 drive system
Chassis format
7
■
Overview
(continued)
Painted modules
The following devices are equipped as standard with coated
modules:
•
Blocksize format units
•
Booksize format units
•
Chassis format units
•
Control Units
•
Sensor Modules
•
Terminal Modules
•
Advanced Operator Panel (AOP30)
The coating on the modules protects the sensitive SMD com-
ponents against corrosive gases, chemically active dust and
moisture.
Nickel-plated busbars
All of the copper busbars used are nickel-plated in order to
achieve the best possible immunity to environmental effects.
Further, it is possible to eliminate having to clean the contacts at
the customer connections, which is required for bare copper
connections.
Note:
For some components, parts of the copper busbars cannot be
nickel-plated for technical reasons.
■
Function
Communication with higher-level controller and customer
terminal block
As customer interface to a higher-level control, as standard there
is a PROFIBUS or PROFINET communication interface on the
Control Unit CU320-2; there are also expansions such as the
Terminal Module TM31, the Terminal Board TB30 and modules
to communicate via CANopen or EtherNet/IP.
These interfaces can be used to connect the system to the
higher-level controller using analog and digital signals, or to
connect additional units.
For additional information, please refer to the SINAMICS Low
Voltage Engineering Manual.
Open-loop and closed-loop control functions
SINAMICS S120 can use a dynamic, high-precision closed-loop
vector control (drive object type VECTOR), or a highly dynamic
closed-loop servo control (drive object type SERVO).
Software and protective functions
The software functions available as standard are described
below:
Software and protective
functions
Description
Setpoint input
The setpoint can be specified both internally and externally; internally as a fixed setpoint, motorized potentiometer setpoint or
jog setpoint, externally via the communications interface or an analog input. The internal fixed setpoint and the motorized
potentiometer setpoint can be switched or adjusted via control commands from any interface.
Motor identification
The automatic motor identification function makes commissioning faster and easier and optimizes closed-loop control of the
drive.
Ramp-function generator
A user-friendly ramp-function generator with separately adjustable ramp-up and ramp-down times, together with adjustable
rounding times in the lower and upper speed ranges, allows the drive to be smoothly accelerated and braked. This results in a
good speed control response and contributes to the reduction of stress on the mechanical system. The down ramp can be
parameterized separately for a quick stop.
V
dc max
controller
The V
dc max
controller automatically prevents overvoltages in the DC link, if the set down ramp is too short, for example.
This may also extend the set ramp-down time.
Note:
This function only makes sense for single-axis applications.
Kinetic buffering (KIP)
For brief line supply failures, the kinetic energy of the rotating drive is used to buffer the DC link and therefore prevents fault
trips. The drive converter remains operational as long as the drive can provide regenerative energy as a result of its motion and
the DC link voltage does not drop below the shutdown threshold. When the line supply recovers within this time, the drive is
again bumplessly accelerated up to its setpoint speed.
Automatic restart
The automatic restart switches the drive on again when the power is restored after a power failure, and ramps up to the current
speed setpoint.
Flying restart
The flying restart function allows the converter to be switched to a motor that is still turning. With the voltage sensing capability
provided by the optional VSM10, the flying restart time for large induction motors can be significantly reduced because the
motor does not need to be de-magnetized.
Technology controller (PID)
Using the technology controller (PID controller) function module, level or flow controls and complex tension controls can be
implemented, for example. The existing D component can act both on the system deviation well as on the actual value (factory
setting). The P, I, and D components are set separately.
Free function blocks (FFB)
Using the freely programmable function blocks, it is easy to implement logic and arithmetic functions for controlling the
SINAMICS drive. The blocks can be programmed at the operator panel or the STARTER commissioning tool.
Drive Control Chart (DCC)
Drive Control Chart (DCC) is an additional tool for the easy configuration of technological functions for SINAMICS. The block
library contains a large selection of control, arithmetic and logic blocks as well as extensive open-loop and closed-loop control
functions. The user-friendly DCC editor enables easy graphics-based configuration, allows control loop structures to be clearly
represented and provides a high degree of reusability of charts that have already been created. DCC is an add-on for the
STARTER commissioning tool (
see Section Engineering tools
).
SINAMICS Technology
Extensions
(SINAMICS TEC)
The SINAMICS TEC are configurable functions or Siemens technologies that can be added to extend firmware functions.
These extensions are designed to allow implementation of highly complex, application-specific tasks for various sectors – such
as storage and retrieval machines.
Additional information about Technology Extensions (TEC) is provided in Section Technology functions.
I
2
t sensing for motor
protection
A motor model stored in the converter software calculates the motor temperature based on the current speed and load.
More exact measurement of the temperature, which also takes into account the influence of the ambient temperature, is
possible by means of direct temperature measurement using KTY84 sensors in the motor winding.
Motor temperature
evaluation
Motor protection by evaluating a KTY84, Pt1000, PTC or Pt100 temperature sensor. When a KTY84 temperature sensor is
connected, the limit values can be set for alarm or shutdown. When a PTC thermistor is connected, the system reaction to
triggering of the thermistor (alarm or trip) can be defined.
© Siemens AG 2017