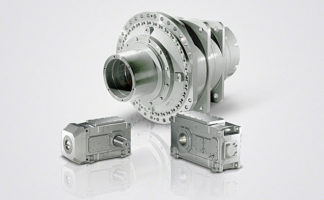
5/20
Siemens D 31 N · March 2016
SINAMICS G120 standard inverters
0.37 kW to 250 kW (0.5 hp to 400 hp)
Control Units
5
■
Overview
CU250S-2 Control Units
CU250S-2 Control Unit
The Control Unit performs closed-loop control functions for the
inverter.
The CU250S-2 Control Units are designed as standard Control
Units for all of the usual applications involving V/f or vector
control.
CU250S-2 Control Units can be used to implement all common
applications involving V/f or vector control as well as applications
for drives with positioning requirements. This expansion allows
them to be used in lifting, swiveling, traversing or rotating applica-
tions. The positioning functionality is comparable with
SINAMICS S110 servo drives.
Two points must be noted here:
•
Vector control (VC) and sensorless vector control (SLVC) are
possible
•
Positioning possible via one encoder or in parallel using two
encoders
The CU250S-2 Control Units can be combined with the following
Power Modules:
• PM240-2
• PM240
• PM250
Note:
Shield plates and shield connection kits are available for use in
the wiring installation of Control Units and Power Modules to
ensure that it complies with EMC guidelines.
For further information about shield connection kits and shield
plates for Control Units and Power Modules, please refer to
section "Supplementary system components".
Safety Integrated functions
The following Safety Integrated Basic Functions (certified
according to IEC 61508 SIL 2 and EN ISO 13849-1 PL d and
Category 3) are integrated as standard in the CU250S-2 series:
•
Safe Torque Off (STO)
to protect against active movement of the drive
•
Safe Stop 1 (SS1)
for continuous monitoring of a safe braking ramp
•
Safe Brake Control (SBC) is used to safely control a holding
brake
The following Safety Integrated Extended Functions (certified
according to IEC 61508 SIL 2 and EN ISO 13849-1 PL d and
Category 3) are optionally available for the CU250S-2 series:
•
Safely Limited Speed (SLS)
for protection against dangerous movements on exceeding a
speed limit
•
Safe Direction (SDI)
This function ensures that the drive can only rotate in the
selected direction.
•
Safe Speed Monitor (SSM)
This function signals if a drive operates below a specific
speed/feed velocity.
These functions can be activated by means of PROFIsafe or via
the safety inputs.
None of the safety functions require a motor encoder and they
are thus much cheaper and easier to implement. Existing sys-
tems in particular can be simply updated with safety technology
without the need to change the motor or mechanical system.
The Safe Torque Off (STO) function can be used without restric-
tion for all applications. The SS1, SLS, SDI and SSM functions
are only permissible for applications where the load can never
accelerate when the inverter is switched off. They are therefore
not permitted for applications involving pull-through loads such
as hoisting gear and unwinders.
Additional information is provided in chapter Highlights,
section Safety Integrated.
© Siemens AG 2016