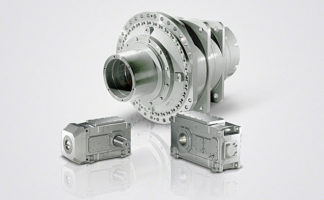
Appendix
SINAMICS GM150, SINAMICS SM150
Glossary
11/2
Siemens D 12 · 2012
11
■
Overview
Active infeed
Overall functionality of an infeed with
→
Active Line Module,
including the required additional components (filters, switching
devices, computing power portion of a
→
Control Unit, voltage
detection, etc.).
For cabinet-mounted units, a
→
Motor Module can be used
instead of the
→
Active Line Module.
Active Line Module
A controlled, self-commutated infeed/regenerative feedback
unit (with IGBTs in infeed/feedback direction) which supplies a
constant DC link voltage for the
→
Motor Modules.
Induction motor
The induction motor is an AC motor, which runs at a speed
"lagging behind" the synchronous speed.
Induction motors can be connected to the AC line both directly
in a star or delta circuit and via a converter.
When combined with a converter, induction motors form a
"variable-speed drive system".
Other commonly used terms: squirrel-cage motor, cage motor.
See also
→
Synchronous motor.
Output reactor
Reactor (inductance) at the converter or inverter output for
reducing the capacitive charge/discharge currents in long
power cables.
Basic infeed
Overall functionality of an infeed with
→
Basic Line Module
including the required additional components (filters, switching
devices, etc.).
Basic Line Module
Unregulated line infeed unit (diode bridge or thyristor bridge,
without feedback) for rectifying the line voltage for the DC link.
CompactFlash Card
Memory card for non-volatile storage of the drive software and
corresponding parameters. The memory card can be plugged
into the
→
Control Unit from the outside.
Control Unit
The central control module, in which the open-loop and
closed-loop control
functions for one or more SINAMICS
→
Line Modules
and/or
→
Motor Modules are implemented.
DRIVE-CLiQ
Abbreviation for "Drive Component Link with IQ".
Communication system for connecting the various components
of a SINAMICS drive system, e.g.
→
Control Unit,
→
Line
Modules,
→
Motor Modules, motors and speed/position
encoders.
From a hardware perspective, DRIVE-CLiQ is based on the
standard Industrial Ethernet with twisted-pair cables. The
DRIVE-CLiQ line provides the transmit and receive signals
and also the +24 V power supply.
Field weakening
Field weakening describes the reducing of the magnetizing
current of an electric motor in order that the speed can be
increased further when the rated voltage is reached.
Non-Siemens motor
A motor is designated as a non-Siemens motor if its motor data
is not known to the drive line-up, and it cannot be identified by
means of its order number.
The motor data of an external motor is required for commission-
ing. It must be entered manually in the corresponding parame-
ters.
Kinetic buffering
Kinetic buffering (KIP) is a software function, which can be used
to bridge transient line failures (up to approx. 1 s or as long as
the drive continues to turn). Kinetic buffering can usually only be
used on drives that are primarily motor-driven. It requires a suffi-
ciently large centrifugal mass, i.e., sufficient kinetic energy, on
the part of the mechanical transmission element. During the line
failure, KIP switches the machine to no-load operation or light re-
generation (in order to cover the minor losses from the motor and
inverter). Once the line supply has been restored, the machine
switches back to standard motor-driven operation.
In order to use kinetic buffering, the technological conditions
must be in place to allow the motor to coast or brakes for the
duration of the line failure. In some applications with multi-motor
drives, the speed ratios between the individual drives have to be
maintained during kinetic buffering, in order to prevent the web
from tearing or damage. In such cases, kinetic buffering may
only be activated on one of the drives (usually the main drive).
The reduced speed setpoint values must then be fed into the
overall setpoint cascade.
© Siemens AG 2012