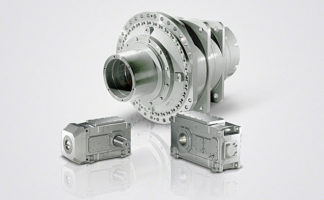
Engineering information
SINAMICS GM150, SINAMICS SM150
Motors
9/16
Siemens D 12 · 2012
9
■
Configuration
Operation of motors with several winding systems
To increase the output power of the converters it is possible to
operate several power units in parallel. In this way, a maximum
power rating of up to 13 MVA with an output voltage of 4.16 kV
can be achieved by connecting two SINAMICS GM150 in the
IGBT version converters in parallel. Using the same principle, a
maximum power rating of 21 MVA or 31.5 MVA is achieved by
connecting three SINAMICS GM150, in the IGCT version and
SINAMICS SM150 converters in parallel.
To ensure a uniform division of current between the two sub-
systems, two or three electrically isolated but mutually non-
displaced winding systems are required in the motor.
Operation of two-pole motors
High-speed converter drives with 2-pole motors require special
measures regarding their mechanical design (limiting and
critical speed, bearings, rotor design, foundation design).
An inquiry is required for such applications.
In the case of retrofit applications it is necessary to ensure that
the motors have no mechanical natural resonance in the pro-
vided setting range. Affected speed ranges can be suppressed
by the converter if necessary.
Operation of explosion-protected motors
Motors from Siemens are also available in versions for use in
areas subject to explosion hazard. Types of protection available
for the motors are:
•
Pressurized enclosure: Ex pe IIC T3
acc. to EN 60079-2/VDE 0170/0171 T301 (IEC 60079-2)
•
Non-sparking: Ex n AIIC T3
acc. to EN 60079-15/VDE 0170/0171 T16 (IEC 60079-15)
Apart from the measures required – also for fixed-speed motors
– to increase the type of protection, for variable speed motors
it is also necessary to have a shaft grounding device with type
of protection type Ex d IIC T6 (without rotary pulse encoder) or
Ex de IIC T6 (with rotary pulse encoder).
An inquiry is always necessary for motors with increased safety
Ex e.
Ex certification
For motors with Ex n type of protection and converter operation
it may be necessary to accept the complete system on a case-
for-case basis in order to issue an Ex certificate. An inquiry is
required for such cases.
An acceptance test of the complete drive system is not required
for motors with Ex pe type of protection and converter operation.
Drives for a square-law load torque
Driven loads with a square-law load torque (
M
~
n
2
) such as
pumps and fans, require the full torque at rated speed. In-
creased starting torques or load surges do not usually occur.
It is therefore unnecessary to provide an overload capability for
the converter.
The following applies when selecting a suitable converter for
driven loads with a square-law load torque: The rated current of
the converter must be at least as large as the motor current at full
torque in the required load point.
Drives for a constant load torque
Self-ventilated motors cannot provide their full rated torque in
continuous operation over the complete speed range. The con-
tinuous permissible torque decreases as the speed decreases
because of the reduced cooling effect. Depending on the speed
range, the torque – and thus the power – must be reduced
accordingly for self-cooled motors.
For frequencies above the rated frequency
f
N
, force-ventilated
motors are operated in the field-weakening mode. In this case,
the torque that can be utilized decreases with approx.
f
N
/
f
. The
power remains constant. A sufficient interval of
≥
30 % from the
breakdown torque must be observed, which is reduced by
(
f
N
/
f
)
2
.
Drives with overload requirements
The rated data of the converters specified in the Technical data
provide no reserves for overload capability. The current rating
of the converter must always be reduced if the specifications
call for an increased overload capability of the converter. The
required power reduction differs according to the application,
operating mode and converter type. The derating can be deter-
mined on request if all of the boundary conditions are specified.
Operating standard line motors
(only SINAMICS GM150 in the IGBT version)
In conjunction with the optional sine-wave filter (option
Y15
) the
SINAMICS GM150 as IGBT version is ideal for the operation of
line motors in applications with a quadratic load torque (e.g.
pumps and fans). The near sinusoidal output voltages and cur-
rents rule out all loading of the insulating system and bearings.
The sine-wave filters supply the motors with almost sinusoidal
motor currents and voltages so that line motors can be operated.
The sine-wave filter operates optimally for motors with a rated
frequency of 50 Hz or 60 Hz. It should be noted that only driven
loads with a square-law load torque may be operated (e.g.
pumps, fans). The output frequencies used in operation can lie
in the range between 30 Hz and 66 Hz.
A field weakening range of 1:1.1 is permissible (max. 55 Hz for
50 Hz motors and max. 66 Hz for 60 Hz motors).
The voltage harmonic distortion at an output frequency of 50 Hz
is less than 5 % when using a sine-wave filter.
In order to optimally adapt the sine-wave filter to the motor, the
rated motor current, the motor current at the rated point and the
motor no-load current must be specified when ordering.
© Siemens AG 2012