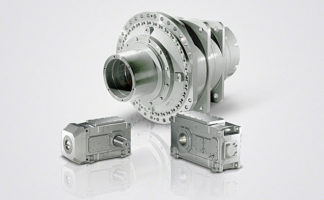
Engineering information
SINAMICS GM150, SINAMICS SM150
Motors
9/15
Siemens D 12 · 2012
9
■
Configuration
General notes on operating high-voltage motors
High-voltage motors can generate a voltage if they are driven by
the load as a result of the inherent plant or system principle. The
magnitude of this voltage essentially depends on the speed and
the type of excitation of the high-voltage motor. The following
must be noted in order to ensure that the converter power unit
safely and reliably operates while the high-voltage motor is
rotating:
•
For permanent-magnet synchronous motors, options
L49
(make-proof grounding switch at the converter output) and
L52
(circuit breaker at the converter output) must
be selected.
•
For induction motors and separately-excited synchronous
motors, if the motor is driven by the load, then options
L49
and
L51/L52
(depending on the particular application) should
be
selected.
Operation of Siemens high-voltage motors
A sine-wave filter is not required between the Siemens high-
voltage motors H-compact, H-compact PLUS, H-modyn and
special motors for e.g. marine, rolling mill and high-speed
applications and the SINAMICS GM150 and SINAMICS SM150
converters. Reliable operation of the drive is assured by the
following measures:
•
The MICALASTIC VPI insulation system is optimally suited for
the voltage stressing which occurs in converter operation.
•
The protection concept for high voltage motors when fed from
converters involves two insulating bearings to avoid damag-
ing bearing currents. Further, shaft grounding is absolutely
necessary so that no voltage can be established at the motor
shaft with respect to ground. The shaft is either grounded
using a rotary pulse encoder with integrated grounding track
on the non-drive end or using a separate grounding brush on
the motor drive end. In the first case, an insulated coupling
must be used. This is because as a result of the shaft ground-
ing at the non-drive end, circulating currents can flow through
the driven load. In the second case, the rotary pulse encoder
must be mounted at the non-drive end so that it is insulated;
an insulated coupling is not required
(see alongside figures)
.
Minimum motor rated frequency:
•
SINAMICS GM150 in IGBT version and
SINAMICS SM150 in IGBT version:
20 Hz
•
SINAMICS GM150 in IGCT version and
SINAMICS SM150 in IGCT version:
- 8.5 Hz for an output voltage of 3.3 kV
- 5.0 Hz for a reduced voltage of 3.15 kV
Note:
Please contact your regional Siemens sales partner in the
case of different data.
Note
:
For motors with rated frequency of less than 8.5 Hz, a reduced
voltage of 3.15 kV should always be selected.
Shaft grounding at the non-drive end
Shaft grounding at the drive end
Insulated
coupling
Load
Insulated
coupling
Shaft grounding
Rotary pulse encoder
Motor
Insulated bearing
Load
Shaft grounding
Rotary pulse encoder
Motor
Motor
G_D012_EN_00048
Load
Coupling
Shaft grounding
Rotary pulse encoder
Motor
Insulated bearing
Load
Coupling
Shaft grounding
Rotary pulse encoder
Motor
Motor
G_D012_EN_00049
© Siemens AG 2012