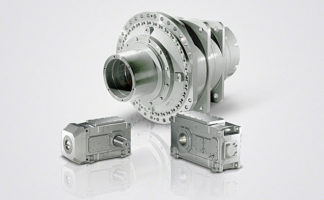
Engineering information
SINAMICS GM150, SINAMICS SM150
Circuit breakers
9/10
Siemens D 12 · 2012
9
■
Configuration
The circuit breaker placed on the primary side of the input trans-
former on the plant side belongs to the safety system of the con-
verter. If a fault occurs inside the converter, the energy that is
effective at the fault location must be limited. This is realized as
a result of the inductance of the incoming transformer, which
limits the rate-of-rise and magnitude of the current and the circuit
breaker that trips as quickly as possible.
For the above conditions to be satisfied, the circuit breaker used
must have the following characteristics:
•
The total opening time of the circuit breaker – from the
command to actually opening – must not be more than 80 ms.
This means that the opening time, specified in the technical
documentation of the circuit breaker manufacturer, must not
be longer than 80 ms. The converter monitors the total
opening time.
•
The converter monitors the TRIP coils (shunt releases) for wire
breakage and failure of the control voltage in the switchgear
installation.
•
The circuit breaker must be fitted with an undervoltage trip
unit. The undervoltage trip unit (low-voltage coil) is controlled
by way of the tripping chain in which the "undervoltage trip
unit" of the converter must also be integrated. The auxiliary
voltage from the switchgear (this is a reliable supply) is used
as the supply.
•
Additional delay times in controlling the circuit breaker must
be avoided. All commands from the converter to the circuit
breaker must act directly, without recourse to any coupling
relays.
•
A separate check-back signal must exist for each of the circuit
breaker states ON and OFF. The checkbacks must not be
delayed, i.e. no coupling relays may be used.
•
An additional, independently operating overcurrent protection
for the circuit breaker must be provided on the plant side
(transformer and cable protection).
•
Under no circumstances may the circuit breaker be electri-
cally or mechanically closed externally. A mechanical inter-
lock of the manual ON command on the circuit breaker
prevents destruction of the converter by uncoordinated
switch-on.
■
Configuration
The SINAMICS GM150 and SINAMICS SM150 converters are
always connected to the medium-voltage network through a
converter transformer.
By using the transformer the drive (converter and motor) are
disconnected from the network and electrically isolated:
•
The short-circuit power is limited to a maximum permissible
value.
•
Converter and motor are operated ground-free.
•
The line harmonics and the voltage ripple are limited.
An insulation monitor, integrated in the converter, monitors the
insulation state of the transformer secondary winding up to the
motor.
Configurations for SINAMICS GM150
For the 12-pulse Basic Line Module of the SINAMICS GM150
converter, a three-winding transformer is required. The second-
ary windings of the three-winding transformer have a phase shift
around 30°el, resulting in a 12-pulse infeed with accordingly
lower line harmonic distortions.
For the 24-pulse Basic Line Module, two three-winding trans-
formers are required. Two transformers with primary windings
offset through 15° are used.
In this case, it must be ensured that the individual secondary
windings have the same voltage, in order to reduce the line
harmonics and to ensure a symmetrical current distribution. In
this case, a maximum deviation of 1 % is permissible for the two
secondary windings connected in parallel.
Instead of the two three-winding transformers a five-winding
transformer can also be used in consultation with the trans-
former manufacturer.
Configurations for SINAMICS SM150
A two-winding transformer is required for each Active Line
Module. When two or three complete converter units are oper-
ated in parallel, it is also possible to use a three-winding or a
four-winding transformer with offset windings to suppress line
harmonics.
Transformers
© Siemens AG 2012