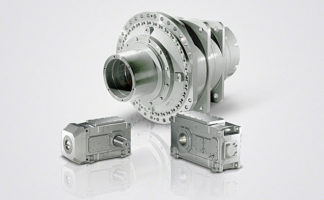
SINAMICS SM150
Medium-Voltage Converter
SINAMICS SM150 in IGCT version
5/8
Siemens D 12 · 2012
5
■
Function
Characteristic features
Software and protection functions
SINAMICS SM150 in the IGCT version
Line Module (rectifier on mains side)
Active Line Module
(four-quadrant operation)
Standard
Motor Module (rectifier on motor side)
Voltage range
3.3 kV
Power range (typ.)
5 ... 31.5 MVA
Cooling method
• Water cooling
Standard
Control modes
Standard: With encoder
• Induction motor
Standard
• Synchronous motor,
separately excited
Option
• Synchronous motor, separately
excited, with brushless
excitation system
On request
• Synchronous motor,
permanently excited
Option
DC bus configuration with several
Motor Modules on one common
DC bus
Standard
SINAMICS SM150
in the IGCT version
Description
Closed-loop control
The motor-side closed-loop control is realized as a field-oriented closed-loop vector control that can be
operated as a speed or torque control as required. The closed-loop vector control achieves the dynamic
performance of a DC drive. This is made possible by the fact that the current components forming the torque
and flux can be controlled precisely independently of each other. Prescribed torques can thus be observed
and limited accurately. In the speed range from 1:10, the field-oriented closed-loop control does not require
an actual speed value encoder.
An actual speed value encoder is required in the following scenarios:
• High dynamics requirements
• Torque control/constant torque drives with a control range > 1:10
• Very low speeds
• Very high speed accuracy
Setpoint input
The setpoint can be defined internally or externally; internally as a fixed setpoint, motorized potentiometer
setpoint or jog setpoint, externally via the PROFIBUS interface or an analog input of the customer's terminal
strip. The internal fixed setpoint and the motorized potentiometer setpoint can be switched over or adjusted
using control commands via all interfaces.
Ramp-function generator
A user-friendly ramp-function generator with separately adjustable ramp-up and ramp-down times, together
with variable smoothing times in the lower and upper speed ranges, improves the control response and
therefore prevents mechanical overloading of the drive train. The ramp-down ramps can be parameterized
separately for emergency stop.
V
dc max
controller
The V
dc max
controller automatically prevents overvoltages in the DC link if the down ramp is too short, for
example. This can also extend the set ramp-down time.
Kinetic buffering (KIP)
Power supply failures are bridged to the extent permitted by the kinetic energy of the drive train. The speed
drops depending on the moment of inertia and the load torque. The current speed setpoint is resumed when
the power supply returns.
Automatic restart
The automatic restart switches the drive on again when the power is restored after a power failure or a general
fault, and ramps up to the current speed setpoint.
Flying restart
The flying restart function permits smooth connection of the converter to a rotating motor.
Diagnostics functions
• Self-diagnosis of control hardware
• Non-volatile memory for reliable diagnosis when the power supply fails
• Monitoring the IGCTs with individual messages for each mounting location
• User-friendly on-site operator panel with plain text messages
Operating hours and switching
cycle counter
The switching cycles of the circuit breakers are detected and summed to form the basis for preventive main-
tenance work.
Operator protection
The cabinet doors of the power units are fitted with electromagnetic locks. This prevents the cabinet doors
being opened while hazardous voltages are connected inside the cabinet.
© Siemens AG 2012