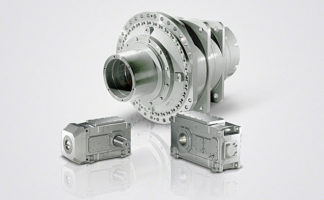
SINAMICS G180
Services and documentation
Industry Services
for the entire life cycle
6/15
Siemens D 18.1 · 2014
6
■
Overview
(continued)
Service Contracts:
A service contract ensures the high level of reliability that you
simply need today in industry.
Tailored service packages for the maintenance ensure minimal
downtimes and reduce the maintenance budget. The possibili-
ties of remote maintenance ensure an additional valuable
reliability plus.
Modular service contracts for electric motors and converters
Individually agreed service contracts make the maintenance,
optimization and modernization of automation and drive tech-
nology in industry more efficient and dynamic coupled with
reduced costs. Flexible options, such as extended service
periods, defined arrival times and special maintenance intervals
or remote maintenance can be defined to meet your specific
requirements. In combination with the extensive experience and
know-how of maintenance and service specialists from Siemens
Industry Services, you can achieve reduced downtime,
plannable operating costs and a high availability of all machines
and equipment.
Maintenance contracts for motors and converters
Reliable motors and converters are the core of every industrial
plant. With uninterrupted duty and poor environmental condi-
tions (dirt, dust and aggressive atmosphere), individual compo-
nents such as pulse encoders, roller bearings and fans are sub-
ject to greater wear: whereby small-scale local damage, such as
a reduction in insulation resistance, can cause considerable
secondary damage. To prevent this, maintenance contracts from
Siemens offer fixed maintenance and service intervals in which
the status of all components can be checked by specialists and
critical components can be replaced. The corresponding docu-
mentation and product-specific checklists help to perform all the
relevant investigations at the right time and achieve optimum
availability.
The maintenance contract also includes a comprehensive con-
sultation with a view to maximizing plant availability and assess-
ing the contribution that could be made by conversion and
refitting in the area of drives. In parallel with this, Siemens
ensures with plant-specific instructions during on-site service
that plant operators are able to reliably master all operations and
simple maintenance tasks. Siemens also offers more advanced
training courses with the objective of preventative maintenance.
When the maintenance contract is drawn up, the customer
profits from comprehensive advice and numerous, optional
services:
•
Defined product support/maintenance
•
Training (basic and advanced)
•
Remote services and condition monitoring
•
Plant support remotely by telephone
•
Specified support times (response, arrival and service times)
•
Customized spare parts packages on site
•
Defined costs
Remote Services – expert knowledge within your grasp
Remote Services can be integrated into service contracts as an
optional service. The Remote Service platform from Siemens
(cRSP) has set new standards in IT security, traceability and
flexibility. This also enables complex drive systems to be moni-
tored, analyzed and optimized if required by means of remote
access from Siemens drive specialists efficiently and reliably.
The breadth of supported services ranges from reading the
archived log and analyzing stored data through online condition
monitoring for motors and software updates as far as video
support with service work on site.
Condition Monitoring – for condition-based maintenance
With Siemens service contracts, it is possible to select condition
monitoring for central drive components and those subject to
wear as an optional service. This means that irregularities in
operation can be detected at an early stage so that counter-
measures can be initiated and service work can be planned
more efficiently. In the case of motors, the emphasis is on the
monitoring of vibration, winding and bearing temperatures as
well as speed. In the case of frequency converters, monitoring is
concentrated on current, voltage and power, cabinet tempera-
ture, water temperature and heatsink temperature, fault pattern
and communication.
© Siemens AG 2014