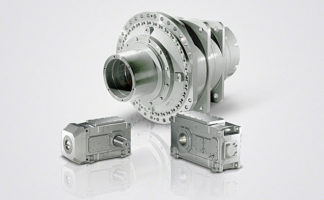
SINAMICS G180
Configuring instructions
Cable cross-sections and connections
5/15
Siemens D 18.1 · 2014
5
■
Overview
(continued)
Current-carrying capacity according to IEC 60364-5-52 at 40 °C
With higher amperages, cables must be connected in parallel.
Note:
The recommendations for the North American market in AWG or MCM must be taken from the appropriate NEC (National Electrical
Code) and/or CEC (Canadian Electrical Code) standards.
Grounding and PE conductor cross-section
The PE conductor must be dimensioned to meet the following
requirements:
•
In the case of a ground fault, no impermissibly high contact
voltages resulting from voltage drops on the PE conductor
caused by the ground fault current may occur (< 50 V AC or
< 120 V DC, IEC 61800-5-1, IEC 60364, IEC 60543).
•
The PE conductor should not be excessively loaded by any
ground fault current it carries.
•
If it is possible for continuous currents to flow through the PE
conductor when a fault occurs, the PE conductor cross-
section must be dimensioned for this continuous current.
•
The PE conductor cross-section should be selected accord-
ing to IEC 60204-1, IEC 60439-1, IEC 60364.
Note:
The recommendations for the North American market in AWG
or MCM must be taken from the appropriate NEC (National
Electrical Code) and/or CEC (Canadian Electrical Code)
standards.
•
Switchgear and motors are usually grounded separately via
separate local ground connections. When this grounding
arrangement is used, the current caused by a ground fault
flows through the parallel ground connections and is divided.
Despite the use of the relatively small PE conductor cross-
sections specified in the table above, no impermissible con-
tact voltages can develop with this grounding system. Based
on experience with different grounding configurations, how-
ever, we recommend that the ground wire from the motor
should be routed directly back to the converter. For EMC
reasons and to prevent bearing currents, symmetrical 3-wire,
three-phase cables should be used where possible instead of
4-wire cables, especially on drives in the higher power range.
The protective or PE conductor must be routed separately
when 3-wire cables are used or must be arranged symmetri-
cally in the motor cable. The symmetry of the PE conductor is
achieved using a conductor surrounding all phase conductors
or using a cable with a symmetrical arrangement of the three
phase conductors and three ground conductors.
•
Through their high-speed controllers, the converters limit the
load current (motor and ground fault currents) to an rms value
corresponding to the rated current. We therefore recommend
the use of a PE conductor cross-section analogous to the
phase conductor cross-section for grounding the control
cabinet.
Cross-section 3-wire cable
3-wire copper cable
3-wire aluminum cable
Single routing
Groups of cables
routed in parallel
1)
Single routing
Groups of cables
routed in parallel
1)
mm²
A
A
A
A
3 × 2.5
22
17
17
13
3 × 4.0
30
23
23
18
3 × 6.0
37
29
29
22
3 × 10
52
41
40
31
3 × 16
70
54
53
41
3 × 25
88
69
68
53
3 × 35
110
86
84
65
3 × 50
133
104
102
79
3 × 70
171
133
131
102
3 × 95
207
162
159
124
3 × 120
240
187
184
144
3 × 150
278
216
213
166
3 × 185
317
247
244
190
3 × 240
374
292
287
224
3 × 300
432
337
331
259
Cross-section of the
phase conductor
Minimum cross-section of external PE
conductor
mm
2
mm
2
≤
16
Minimum phase conductor cross-section
16 ... 35
16
≥
35
Minimum half the phase conductor
cross-section
1)
Maximum 9 cables may be routed horizontally in direct contact with one
another on a cable rack (reduction factor 0.68).
© Siemens AG 2014