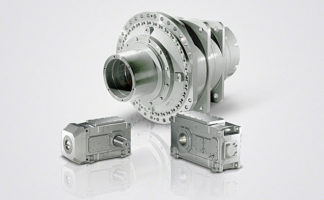
SINAMICS G180
Configuring instructions
Cable cross-sections and connections
5/14
Siemens D 18.1 · 2014
5
■
Overview
(continued)
Converter connection for different pulse numbers
Required cable cross-sections for line and
motor connections
In order to ensure compliance with the EMC Directive, it is
generally recommended that shielded cables or cables with a
concentric PE conductor of type NYCWY are used to make the
cable connections from the mains supply to the converter and
from the converter to the motor.
Where possible, symmetrical 3-wire three-phase power cables
should be installed between the converter and the motor on
drives in the higher power range. It may be necessary to
connect several of these cables in parallel. There are basically
two reasons for this recommendation:
•
This is the only way in which the high IP55 degree of protection
can be achieved for the motor terminal box without problems,
because the cables enter the terminal box via glands and the
number of possible glands is limited by the geometry of the
terminal box. Therefore single cables are less suitable.
•
With symmetrical 3-wire three-phase cables, the summed
ampere-turns over the cable outer diameter are equal to zero.
They can be routed in conductive, metal cable ducts or racks
without any significant currents (ground currents or leakage
currents) being induced in these conductive metal connec-
tions. The danger of induced leakage currents and thus of
increased cable sheath losses is significantly higher with
single-wire cables.
Dimensioning of connecting cable between mains supply
and converter:
•
The voltage load on the cable should equal at least
V
0
/
V
= 0.6/1 kV.
•
Current load:
- The cable cross-section must be dimensioned in
accordance with the valid standards, e.g. IEC 60364-5-52.
- The mains cable is dimensioned according to the converter
input current (specified on the type plate).
•
Precaution against injury due to indirect contact:
- An overcurrent protective device with additional equipoten-
tial bonding at the motor protects against injury caused by
indirect contact.
•
A neutral conductor is not required.
Dimensioning of connecting cable between converter
and motor:
•
The voltage load on the cable should equal at least
V
0
/
V
= 0.6/1 kV.
•
Current load:
- The cable cross-section must be dimensioned in
accordance with the valid standards, e.g. IEC 60364-5-52.
- The motor cable is dimensioned according to the converter
output current (specified on the type plate).
The required cable cross-section depends on the amperage
which flows through the cable. The permissible current loading
of cables is defined, for example, in IEC 60364-5-52. It depends
on ambient conditions, such as temperature, but also on the
routing method. An important factor to consider is whether
cables are routed singly and are therefore relatively well venti-
lated, or whether groups of cables are routed together. In the
latter instance, the cables are not ventilated so well and might
therefore heat one another to a greater degree. For the relevant
correction factors applicable to these boundary conditions,
please refer to IEC 60364-5-52. The table below provides a
guide to the recommended cross-sections (based on
IEC 60364-5-52) for PVC-insulated, 3-wire copper and alumi-
num cables, a permissible conductor temperature of 70 °C (e.g.
Protodur NYY or NYCWY) and an ambient temperature of 40 °C.
Pulse
number
Line connection on converter
6
Three phases
12
Two transformer secondary systems, each with three
phases, i.e. six phases in total.
Both systems must be phase offset by 30° in each case,
e.g. using the transformer vector group Dy5d6.
Important:
Does not apply to 400 V units owing to the shift transformer
solution – the line connection for these units is made with
three phases.
18
Three transformer secondary systems, each with three
phases, i.e. nine phases in total.
The three systems must be phase offset by 20° in each
case, e.g. using the transformer vector group
Dy0y+20y-20.
24
Four transformer secondary systems, each with three
phases, i.e. twelve phases in total.
The four systems must be phase offset by 15° in each
case, e.g. by two transformers with vector groups
Dy5.25d6.25 and Dy4.75d5.75.
© Siemens AG 2014